ਪੀਸਣ ਵਾਲੀਆਂ ਡਿਸਕਾਂ ਵੱਖ-ਵੱਖ ਉਦਯੋਗਾਂ ਵਿੱਚ ਇੱਕ ਮਹੱਤਵਪੂਰਨ ਭੂਮਿਕਾ ਨਿਭਾਉਂਦੀਆਂ ਹਨ, ਸਮੱਗਰੀ ਨੂੰ ਆਕਾਰ ਦੇਣ ਅਤੇ ਫਿਨਿਸ਼ਿੰਗ ਵਿੱਚ ਸਹਾਇਤਾ ਕਰਦੀਆਂ ਹਨ। ਹਾਲਾਂਕਿ, ਕਿਸੇ ਵੀ ਹੋਰ ਔਜ਼ਾਰ ਵਾਂਗ, ਉਹ ਉਹਨਾਂ ਮੁੱਦਿਆਂ ਤੋਂ ਮੁਕਤ ਨਹੀਂ ਹਨ ਜੋ ਉਹਨਾਂ ਦੀ ਕੁਸ਼ਲਤਾ ਅਤੇ ਪ੍ਰਦਰਸ਼ਨ ਨੂੰ ਰੋਕ ਸਕਦੇ ਹਨ। ਇਸ ਲੇਖ ਵਿੱਚ, ਅਸੀਂ ਆਮ ਪੀਸਣ ਵਾਲੀਆਂ ਡਿਸਕ ਸਮੱਸਿਆਵਾਂ ਵਿੱਚ ਡੂੰਘਾਈ ਨਾਲ ਜਾਵਾਂਗੇ, ਉਹਨਾਂ ਦੇ ਮੂਲ ਕਾਰਨਾਂ ਦੀ ਪੜਚੋਲ ਕਰਾਂਗੇ, ਅਤੇ ਇੱਕ ਸਹਿਜ ਵਰਕਫਲੋ ਲਈ ਪ੍ਰਭਾਵਸ਼ਾਲੀ ਹੱਲ ਪ੍ਰਦਾਨ ਕਰਾਂਗੇ।
ਜਾਣ-ਪਛਾਣ
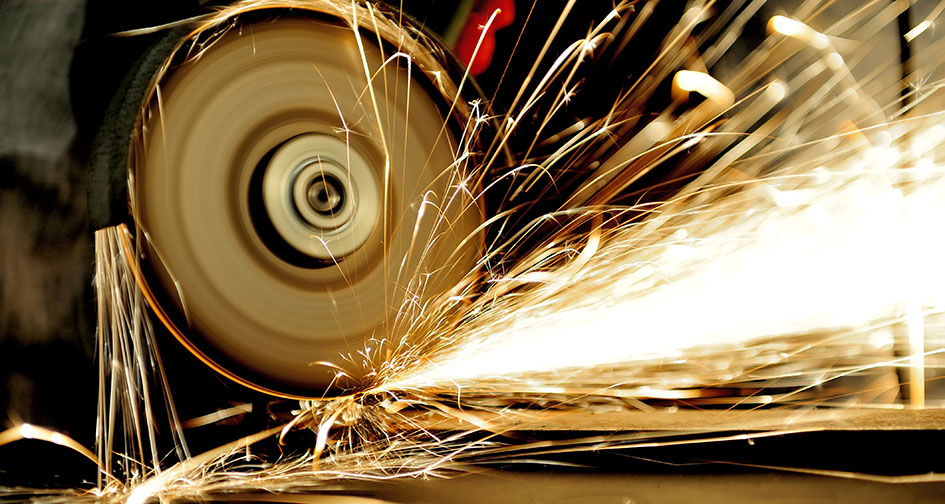
ਪੀਸਣ ਵਾਲੀਆਂ ਡਿਸਕਾਂ ਵੱਖ-ਵੱਖ ਉਦਯੋਗਾਂ ਵਿੱਚ ਇੱਕ ਬੁਨਿਆਦੀ ਭੂਮਿਕਾ ਨਿਭਾਉਂਦੀਆਂ ਹਨ, ਸਮੱਗਰੀ ਨੂੰ ਹਟਾਉਣ, ਆਕਾਰ ਦੇਣ ਅਤੇ ਫਿਨਿਸ਼ਿੰਗ ਪ੍ਰਕਿਰਿਆਵਾਂ ਲਈ ਜ਼ਰੂਰੀ ਸਾਧਨਾਂ ਵਜੋਂ ਕੰਮ ਕਰਦੀਆਂ ਹਨ। ਉਹਨਾਂ ਦੀ ਪਰਿਭਾਸ਼ਾ, ਉਦਯੋਗਾਂ ਵਿੱਚ ਮਹੱਤਵ, ਅਤੇ ਆਮ ਮੁੱਦਿਆਂ ਨੂੰ ਸਮਝਣਾ ਉਹਨਾਂ ਦੀ ਵਰਤੋਂ ਨੂੰ ਅਨੁਕੂਲ ਬਣਾਉਣ ਅਤੇ ਕੁਸ਼ਲ ਕਾਰਜਾਂ ਨੂੰ ਯਕੀਨੀ ਬਣਾਉਣ ਲਈ ਬਹੁਤ ਜ਼ਰੂਰੀ ਹੈ।
A. ਪੀਸਣ ਵਾਲੀਆਂ ਡਿਸਕਾਂ ਦੀ ਪਰਿਭਾਸ਼ਾ
ਪੀਸਣ ਵਾਲੀਆਂ ਡਿਸਕਾਂ ਘਸਾਉਣ ਵਾਲੇ ਔਜ਼ਾਰ ਹਨ ਜੋ ਮਸ਼ੀਨਿੰਗ ਪ੍ਰਕਿਰਿਆਵਾਂ ਵਿੱਚ ਸਮੱਗਰੀ ਦੀਆਂ ਸਤਹਾਂ ਨੂੰ ਕੱਟਣ, ਪੀਸਣ ਜਾਂ ਪਾਲਿਸ਼ ਕਰਨ ਲਈ ਵਰਤੀਆਂ ਜਾਂਦੀਆਂ ਹਨ। ਇਹਨਾਂ ਡਿਸਕਾਂ ਵਿੱਚ ਆਮ ਤੌਰ 'ਤੇ ਇੱਕ ਬੈਕਿੰਗ ਸਮੱਗਰੀ ਨਾਲ ਜੁੜੇ ਘਸਾਉਣ ਵਾਲੇ ਕਣ ਹੁੰਦੇ ਹਨ, ਜੋ ਇੱਕ ਘੁੰਮਦਾ ਔਜ਼ਾਰ ਬਣਾਉਂਦੇ ਹਨ ਜੋ ਵਾਧੂ ਸਮੱਗਰੀ ਨੂੰ ਹਟਾ ਸਕਦਾ ਹੈ, ਸਤਹਾਂ ਨੂੰ ਨਿਰਵਿਘਨ ਕਰ ਸਕਦਾ ਹੈ, ਜਾਂ ਕਿਨਾਰਿਆਂ ਨੂੰ ਤਿੱਖਾ ਕਰ ਸਕਦਾ ਹੈ। ਇਹ ਵੱਖ-ਵੱਖ ਆਕਾਰਾਂ ਅਤੇ ਆਕਾਰਾਂ ਵਿੱਚ ਆਉਂਦੇ ਹਨ, ਹਰੇਕ ਖਾਸ ਐਪਲੀਕੇਸ਼ਨਾਂ ਲਈ ਤਿਆਰ ਕੀਤਾ ਗਿਆ ਹੈ।
B. ਵੱਖ-ਵੱਖ ਉਦਯੋਗਾਂ ਵਿੱਚ ਮਹੱਤਵ
ਧਾਤੂ ਦਾ ਕੰਮ ਕਰਨ ਵਾਲਾ ਉਦਯੋਗ:
ਧਾਤ ਦੇ ਨਿਰਮਾਣ ਅਤੇ ਨਿਰਮਾਣ ਵਿੱਚ, ਧਾਤ ਦੀਆਂ ਸਤਹਾਂ ਨੂੰ ਆਕਾਰ ਦੇਣ, ਡੀਬਰਿੰਗ ਕਰਨ ਅਤੇ ਫਿਨਿਸ਼ ਕਰਨ ਲਈ ਪੀਸਣ ਵਾਲੀਆਂ ਡਿਸਕਾਂ ਬਹੁਤ ਜ਼ਰੂਰੀ ਹਨ। ਇਹਨਾਂ ਨੂੰ ਆਮ ਤੌਰ 'ਤੇ ਐਂਗਲ ਗ੍ਰਾਈਂਡਰ ਨਾਲ ਸਹੀ ਮਾਪ ਅਤੇ ਸਤਹ ਦੀ ਗੁਣਵੱਤਾ ਪ੍ਰਾਪਤ ਕਰਨ ਲਈ ਵਰਤਿਆ ਜਾਂਦਾ ਹੈ।
ਉਸਾਰੀ ਉਦਯੋਗ:
ਉਸਾਰੀ ਪੇਸ਼ੇਵਰ ਕੰਕਰੀਟ ਦੀ ਸਤ੍ਹਾ ਤਿਆਰ ਕਰਨ, ਖੁਰਦਰੇ ਕਿਨਾਰਿਆਂ ਨੂੰ ਸਮਤਲ ਕਰਨ, ਅਤੇ ਪੱਥਰ ਅਤੇ ਕੰਕਰੀਟ ਵਰਗੀਆਂ ਸਮੱਗਰੀਆਂ ਵਿੱਚ ਕਮੀਆਂ ਨੂੰ ਦੂਰ ਕਰਨ ਵਰਗੇ ਕੰਮਾਂ ਲਈ ਡਿਸਕਾਂ ਨੂੰ ਪੀਸਣ 'ਤੇ ਨਿਰਭਰ ਕਰਦੇ ਹਨ।
ਆਟੋਮੋਟਿਵ ਉਦਯੋਗ:
ਆਟੋਮੋਟਿਵ ਸੈਕਟਰ ਵਿੱਚ ਪੀਸਣ ਵਾਲੀਆਂ ਡਿਸਕਾਂ ਔਜ਼ਾਰਾਂ ਨੂੰ ਤਿੱਖਾ ਕਰਨ ਤੋਂ ਲੈ ਕੇ ਧਾਤ ਦੇ ਹਿੱਸਿਆਂ ਨੂੰ ਆਕਾਰ ਦੇਣ ਅਤੇ ਫਿਨਿਸ਼ ਕਰਨ ਤੱਕ ਦੇ ਕੰਮਾਂ ਲਈ ਜ਼ਰੂਰੀ ਹਨ। ਇਹ ਆਟੋਮੋਟਿਵ ਪੁਰਜ਼ਿਆਂ ਦੀ ਸ਼ੁੱਧਤਾ ਅਤੇ ਗੁਣਵੱਤਾ ਵਿੱਚ ਯੋਗਦਾਨ ਪਾਉਂਦੇ ਹਨ।
ਲੱਕੜ ਦਾ ਕੰਮ ਉਦਯੋਗ:
ਲੱਕੜ ਦੇ ਕਾਰੀਗਰ ਲੱਕੜ ਦੀਆਂ ਸਤਹਾਂ ਨੂੰ ਆਕਾਰ ਦੇਣ ਅਤੇ ਸਮਤਲ ਕਰਨ ਲਈ ਪੀਸਣ ਵਾਲੀਆਂ ਡਿਸਕਾਂ ਦੀ ਵਰਤੋਂ ਕਰਦੇ ਹਨ। ਇਹ ਡਿਸਕ ਵਾਧੂ ਸਮੱਗਰੀ ਨੂੰ ਹਟਾਉਣ, ਆਕਾਰਾਂ ਨੂੰ ਸੁਧਾਰਨ ਅਤੇ ਹੋਰ ਮੁਕੰਮਲ ਕਰਨ ਲਈ ਲੱਕੜ ਨੂੰ ਤਿਆਰ ਕਰਨ ਵਿੱਚ ਪ੍ਰਭਾਵਸ਼ਾਲੀ ਹਨ।
ਆਮ ਨਿਰਮਾਣ:
ਪੀਸਣ ਵਾਲੀਆਂ ਡਿਸਕਾਂ ਵੱਖ-ਵੱਖ ਨਿਰਮਾਣ ਪ੍ਰਕਿਰਿਆਵਾਂ ਵਿੱਚ ਉਪਯੋਗ ਲੱਭਦੀਆਂ ਹਨ ਜਿੱਥੇ ਸਮੱਗਰੀ ਨੂੰ ਸਹੀ ਢੰਗ ਨਾਲ ਹਟਾਉਣ ਦੀ ਲੋੜ ਹੁੰਦੀ ਹੈ, ਜੋ ਉੱਚ-ਗੁਣਵੱਤਾ ਵਾਲੇ ਹਿੱਸਿਆਂ ਦੇ ਉਤਪਾਦਨ ਵਿੱਚ ਯੋਗਦਾਨ ਪਾਉਂਦੀ ਹੈ।
C. ਆਮ ਸਮੱਸਿਆਵਾਂ ਦਾ ਸਾਹਮਣਾ ਕਰਨਾ
ਡਿਸਕ ਦਾ ਵਿਅਰ ਅਤੇ ਘ੍ਰਿਣਾ:
ਲਗਾਤਾਰ ਵਰਤੋਂ ਨਾਲ ਪੀਸਣ ਵਾਲੀ ਡਿਸਕ ਦੇ ਟੁੱਟਣ ਅਤੇ ਘਿਸਣ ਦਾ ਕਾਰਨ ਬਣ ਸਕਦਾ ਹੈ, ਜਿਸ ਨਾਲ ਇਸਦੀ ਕਾਰਗੁਜ਼ਾਰੀ ਪ੍ਰਭਾਵਿਤ ਹੋ ਸਕਦੀ ਹੈ। ਕੁਸ਼ਲਤਾ ਬਣਾਈ ਰੱਖਣ ਲਈ ਨਿਯਮਤ ਨਿਰੀਖਣ ਅਤੇ ਬਦਲੀ ਜ਼ਰੂਰੀ ਹੈ।
ਜ਼ਿਆਦਾ ਗਰਮ ਹੋਣਾ:
ਲੰਬੇ ਸਮੇਂ ਤੱਕ ਵਰਤੋਂ ਦੌਰਾਨ ਬਹੁਤ ਜ਼ਿਆਦਾ ਰਗੜਨ ਨਾਲ ਓਵਰਹੀਟਿੰਗ ਹੋ ਸਕਦੀ ਹੈ, ਜਿਸ ਨਾਲ ਡਿਸਕ ਦੀ ਟਿਕਾਊਤਾ ਅਤੇ ਤਿਆਰ ਸਤ੍ਹਾ ਦੀ ਗੁਣਵੱਤਾ ਪ੍ਰਭਾਵਿਤ ਹੋ ਸਕਦੀ ਹੈ। ਸਹੀ ਕੂਲਿੰਗ ਉਪਾਅ ਅਤੇ ਸਮੇਂ-ਸਮੇਂ 'ਤੇ ਬ੍ਰੇਕ ਜ਼ਰੂਰੀ ਹਨ।
ਬੰਦ ਹੋਣਾ:
ਡਿਸਕਾਂ ਨੂੰ ਪੀਸਣ ਨਾਲ ਸਮੱਗਰੀ ਦੀ ਰਹਿੰਦ-ਖੂੰਹਦ ਇਕੱਠੀ ਹੋ ਸਕਦੀ ਹੈ, ਜਿਸ ਨਾਲ ਉਨ੍ਹਾਂ ਦੀ ਪ੍ਰਭਾਵਸ਼ੀਲਤਾ ਘੱਟ ਜਾਂਦੀ ਹੈ। ਨਿਯਮਤ ਸਫਾਈ ਜਾਂ ਐਂਟੀ-ਕਲੌਗਿੰਗ ਵਿਸ਼ੇਸ਼ਤਾਵਾਂ ਵਾਲੀਆਂ ਡਿਸਕਾਂ ਦੀ ਚੋਣ ਇਸ ਸਮੱਸਿਆ ਨੂੰ ਰੋਕਣ ਵਿੱਚ ਮਦਦ ਕਰਦੀ ਹੈ।
ਵਾਈਬ੍ਰੇਸ਼ਨ ਅਤੇ ਵੋਬਲਿੰਗ:
ਅਸੰਤੁਲਨ ਜਾਂ ਅਸਮਾਨ ਘਿਸਾਅ ਦੇ ਨਤੀਜੇ ਵਜੋਂ ਵਾਈਬ੍ਰੇਸ਼ਨ ਜਾਂ ਹਿੱਲਜੁਲ ਹੋ ਸਕਦੀ ਹੈ, ਜੋ ਕਿ ਫਿਨਿਸ਼ ਦੀ ਗੁਣਵੱਤਾ ਅਤੇ ਕਾਰਜ ਦੀ ਸੁਰੱਖਿਆ ਦੋਵਾਂ ਨੂੰ ਪ੍ਰਭਾਵਿਤ ਕਰਦੀ ਹੈ। ਸਹੀ ਸਥਾਪਨਾ ਅਤੇ ਸੰਤੁਲਨ ਬਹੁਤ ਜ਼ਰੂਰੀ ਹੈ।
ਗਲਤ ਡਿਸਕ ਚੋਣ:
ਕਿਸੇ ਖਾਸ ਸਮੱਗਰੀ ਜਾਂ ਐਪਲੀਕੇਸ਼ਨ ਲਈ ਗਲਤ ਕਿਸਮ ਦੀ ਪੀਸਣ ਵਾਲੀ ਡਿਸਕ ਦੀ ਚੋਣ ਕਰਨ ਨਾਲ ਅਕੁਸ਼ਲਤਾ ਅਤੇ ਸੰਭਾਵੀ ਨੁਕਸਾਨ ਹੋ ਸਕਦਾ ਹੈ। ਸਮੱਗਰੀ ਦੀ ਅਨੁਕੂਲਤਾ ਦੇ ਆਧਾਰ 'ਤੇ ਸਹੀ ਚੋਣ ਜ਼ਰੂਰੀ ਹੈ।
ਇਹਨਾਂ ਔਜ਼ਾਰਾਂ 'ਤੇ ਨਿਰਭਰ ਉਦਯੋਗਾਂ ਲਈ ਪੀਸਣ ਵਾਲੀਆਂ ਡਿਸਕਾਂ ਨਾਲ ਜੁੜੀਆਂ ਪਰਿਭਾਸ਼ਾ, ਮਹੱਤਵ ਅਤੇ ਸੰਭਾਵੀ ਚੁਣੌਤੀਆਂ ਨੂੰ ਸਮਝਣਾ ਜ਼ਰੂਰੀ ਹੈ। ਆਮ ਮੁੱਦਿਆਂ ਨੂੰ ਹੱਲ ਕਰਕੇ ਅਤੇ ਸਹੀ ਵਰਤੋਂ ਨੂੰ ਯਕੀਨੀ ਬਣਾ ਕੇ, ਉਦਯੋਗ ਆਪਣੇ-ਆਪਣੇ ਐਪਲੀਕੇਸ਼ਨਾਂ ਵਿੱਚ ਪੀਸਣ ਵਾਲੀਆਂ ਡਿਸਕਾਂ ਦੀ ਪ੍ਰਭਾਵਸ਼ੀਲਤਾ ਨੂੰ ਵੱਧ ਤੋਂ ਵੱਧ ਕਰ ਸਕਦੇ ਹਨ।
ਪੀਸਣ ਵਾਲੀਆਂ ਡਿਸਕਾਂ 'ਤੇ ਘਿਸਣਾ ਅਤੇ ਪਾੜਨਾ
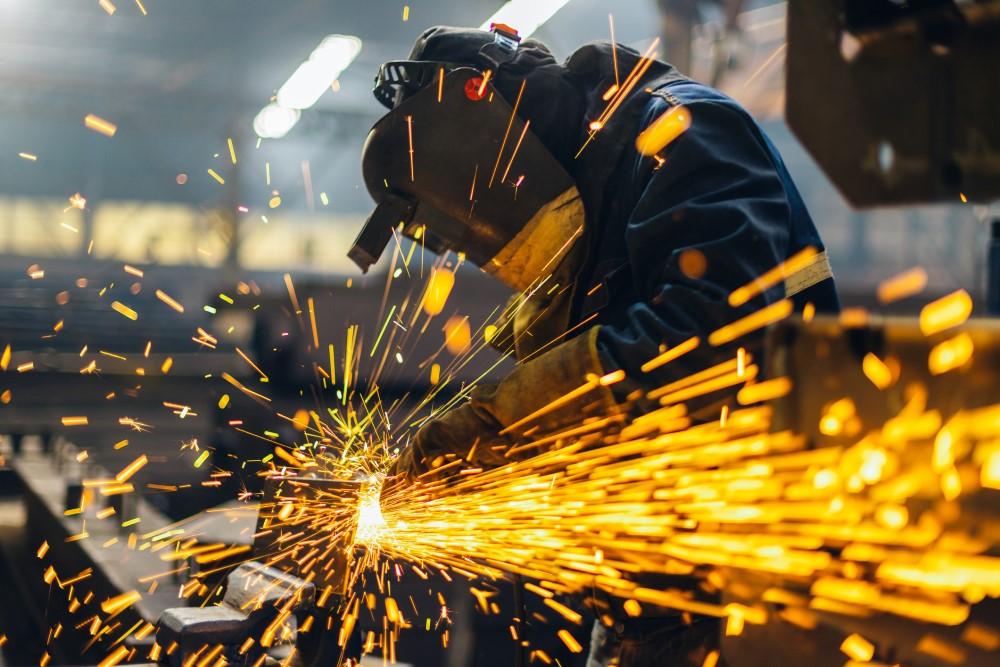
ਪੀਸਣ ਵਾਲੀਆਂ ਡਿਸਕਾਂ ਵੱਖ-ਵੱਖ ਉਦਯੋਗਾਂ ਵਿੱਚ ਜ਼ਰੂਰੀ ਔਜ਼ਾਰ ਹਨ, ਜੋ ਧਾਤ ਦੇ ਨਿਰਮਾਣ ਤੋਂ ਲੈ ਕੇ ਕੰਕਰੀਟ ਪਾਲਿਸ਼ਿੰਗ ਤੱਕ ਦੇ ਕੰਮਾਂ ਲਈ ਜ਼ਰੂਰੀ ਘ੍ਰਿਣਾ ਪ੍ਰਦਾਨ ਕਰਦੀਆਂ ਹਨ। ਪੀਸਣ ਵਾਲੀਆਂ ਡਿਸਕਾਂ ਦੇ ਘਿਸਣ ਅਤੇ ਅੱਥਰੂ ਵਿੱਚ ਯੋਗਦਾਨ ਪਾਉਣ ਵਾਲੇ ਕਾਰਕਾਂ ਨੂੰ ਸਮਝਣਾ ਉਹਨਾਂ ਦੇ ਪ੍ਰਦਰਸ਼ਨ ਨੂੰ ਅਨੁਕੂਲ ਬਣਾਉਣ ਅਤੇ ਸੁਰੱਖਿਆ ਨੂੰ ਯਕੀਨੀ ਬਣਾਉਣ ਲਈ ਬਹੁਤ ਜ਼ਰੂਰੀ ਹੈ।
ਸਮੱਗਰੀ ਦੀ ਕਠੋਰਤਾ ਅਤੇ ਰਚਨਾ:
ਕਠੋਰਤਾ ਭਿੰਨਤਾ:ਪੀਸਣ ਵਾਲੀਆਂ ਡਿਸਕਾਂ ਵੱਖ-ਵੱਖ ਕਠੋਰਤਾ ਪੱਧਰਾਂ ਵਾਲੀਆਂ ਸਮੱਗਰੀਆਂ ਦਾ ਸਾਹਮਣਾ ਕਰਦੀਆਂ ਹਨ। ਧਾਤ ਅਤੇ ਕੰਕਰੀਟ ਵਰਗੀਆਂ ਘ੍ਰਿਣਾਯੋਗ ਸਮੱਗਰੀਆਂ ਦੀ ਕਠੋਰਤਾ ਵਿੱਚ ਕਾਫ਼ੀ ਅੰਤਰ ਹੋ ਸਕਦਾ ਹੈ। ਸਖ਼ਤ ਸਮੱਗਰੀ ਦੇ ਵਿਰੁੱਧ ਲਗਾਤਾਰ ਪੀਸਣ ਨਾਲ ਘਿਸਣ ਤੇਜ਼ ਹੁੰਦੀ ਹੈ।
ਸਮੱਗਰੀ ਰਚਨਾ:ਪੀਸਣ ਵਾਲੀ ਸਮੱਗਰੀ ਵਿੱਚ ਘਿਸਾਉਣ ਵਾਲੇ ਤੱਤਾਂ ਦੀ ਮੌਜੂਦਗੀ ਪੀਸਣ ਵਾਲੀ ਡਿਸਕ ਦੇ ਘਿਸਣ ਨੂੰ ਪ੍ਰਭਾਵਿਤ ਕਰ ਸਕਦੀ ਹੈ। ਘਿਸਾਉਣ ਵਾਲੇ ਕਣ ਡਿਸਕ ਦੇ ਘਿਸਣ ਨੂੰ ਤੇਜ਼ ਕਰ ਸਕਦੇ ਹਨ।
ਪੀਸਣ ਦਾ ਦਬਾਅ ਅਤੇ ਬਲ:
ਬਹੁਤ ਜ਼ਿਆਦਾ ਦਬਾਅ:ਪੀਸਣ ਵਾਲੀ ਡਿਸਕ 'ਤੇ ਬਹੁਤ ਜ਼ਿਆਦਾ ਦਬਾਅ ਪਾਉਣ ਨਾਲ ਜਲਦੀ ਘਿਸਾਈ ਜਾ ਸਕਦੀ ਹੈ। ਡਿਸਕ 'ਤੇ ਬੇਲੋੜੇ ਦਬਾਅ ਤੋਂ ਬਚਣ ਲਈ ਖਾਸ ਐਪਲੀਕੇਸ਼ਨ ਲਈ ਸਿਫ਼ਾਰਸ਼ ਕੀਤੇ ਦਬਾਅ ਦੀ ਵਰਤੋਂ ਕਰਨਾ ਜ਼ਰੂਰੀ ਹੈ।
ਨਾਕਾਫ਼ੀ ਬਲ: ਦੂਜੇ ਪਾਸੇ, ਨਾਕਾਫ਼ੀ ਬਲ ਦੇ ਨਤੀਜੇ ਵਜੋਂ ਲੰਬੇ ਸਮੇਂ ਤੱਕ ਪੀਸਣਾ ਪੈ ਸਕਦਾ ਹੈ, ਵਾਧੂ ਰਗੜ ਅਤੇ ਗਰਮੀ ਪੈਦਾ ਹੋ ਸਕਦੀ ਹੈ, ਜਿਸ ਨਾਲ ਘਿਸਾਅ ਵਧ ਸਕਦਾ ਹੈ।
ਡਿਸਕ ਦੀ ਗੁਣਵੱਤਾ ਅਤੇ ਰਚਨਾ:
ਘਸਾਉਣ ਵਾਲੀ ਸਮੱਗਰੀ ਦੀ ਗੁਣਵੱਤਾ:ਪੀਸਣ ਵਾਲੀ ਡਿਸਕ ਵਿੱਚ ਵਰਤੇ ਜਾਣ ਵਾਲੇ ਘਸਾਉਣ ਵਾਲੇ ਪਦਾਰਥ ਦੀ ਗੁਣਵੱਤਾ ਇਸਦੇ ਜੀਵਨ ਕਾਲ ਨੂੰ ਕਾਫ਼ੀ ਪ੍ਰਭਾਵਿਤ ਕਰਦੀ ਹੈ। ਉੱਚ-ਗੁਣਵੱਤਾ ਵਾਲੇ ਘਸਾਉਣ ਵਾਲੇ ਪਦਾਰਥ ਘਸਾਉਣ ਦਾ ਵਿਰੋਧ ਕਰਦੇ ਹਨ ਅਤੇ ਤਿੱਖਾਪਨ ਨੂੰ ਲੰਬੇ ਸਮੇਂ ਤੱਕ ਬਰਕਰਾਰ ਰੱਖਦੇ ਹਨ।
ਬੰਧਨ ਏਜੰਟ:ਘਿਸਾਉਣ ਵਾਲੇ ਕਣਾਂ ਨੂੰ ਇਕੱਠੇ ਰੱਖਣ ਵਾਲਾ ਬੰਧਨ ਏਜੰਟ ਇੱਕ ਮਹੱਤਵਪੂਰਨ ਭੂਮਿਕਾ ਨਿਭਾਉਂਦਾ ਹੈ। ਇੱਕ ਚੰਗੀ ਤਰ੍ਹਾਂ ਡਿਜ਼ਾਈਨ ਕੀਤਾ ਗਿਆ ਬੰਧਨ ਏਜੰਟ ਡਿਸਕ ਦੀ ਟਿਕਾਊਤਾ ਨੂੰ ਵਧਾਉਂਦਾ ਹੈ।
ਕੰਮ ਦੇ ਵਾਤਾਵਰਣ ਦੀਆਂ ਸਥਿਤੀਆਂ:
ਤਾਪਮਾਨ:ਪੀਸਣ ਦੌਰਾਨ ਪੈਦਾ ਹੋਣ ਵਾਲਾ ਉੱਚ ਤਾਪਮਾਨ ਡਿਸਕ ਦੀ ਰਚਨਾ ਨੂੰ ਪ੍ਰਭਾਵਿਤ ਕਰ ਸਕਦਾ ਹੈ। ਬਹੁਤ ਜ਼ਿਆਦਾ ਗਰਮੀ ਬੰਧਨ ਏਜੰਟ ਨੂੰ ਕਮਜ਼ੋਰ ਕਰਦੀ ਹੈ ਅਤੇ ਘਿਸਣ ਨੂੰ ਤੇਜ਼ ਕਰਦੀ ਹੈ।
ਨਮੀ ਅਤੇ ਦੂਸ਼ਿਤ ਪਦਾਰਥ:ਕੰਮ ਦੇ ਵਾਤਾਵਰਣ ਵਿੱਚ ਨਮੀ ਜਾਂ ਦੂਸ਼ਿਤ ਤੱਤਾਂ ਦੇ ਸੰਪਰਕ ਵਿੱਚ ਆਉਣ ਨਾਲ ਪੀਸਣ ਵਾਲੀ ਡਿਸਕ ਦੀ ਇਕਸਾਰਤਾ ਪ੍ਰਭਾਵਿਤ ਹੋ ਸਕਦੀ ਹੈ, ਜਿਸ ਨਾਲ ਤੇਜ਼ੀ ਨਾਲ ਘਿਸਣ ਲੱਗਦੀ ਹੈ।
ਆਪਰੇਟਰ ਤਕਨੀਕ:
ਸਹੀ ਤਕਨੀਕ:ਆਪਰੇਟਰ ਹੁਨਰ ਅਤੇ ਤਕਨੀਕ ਬਹੁਤ ਜ਼ਰੂਰੀ ਹਨ। ਗਲਤ ਵਰਤੋਂ, ਜਿਵੇਂ ਕਿ ਗਲਤ ਕੋਣਾਂ 'ਤੇ ਪੀਸਣਾ ਜਾਂ ਬਹੁਤ ਜ਼ਿਆਦਾ ਜ਼ੋਰ ਦੀ ਵਰਤੋਂ, ਅਸਮਾਨ ਘਿਸਾਅ ਵਿੱਚ ਯੋਗਦਾਨ ਪਾ ਸਕਦੀ ਹੈ ਅਤੇ ਡਿਸਕ ਦੀ ਲੰਬੀ ਉਮਰ ਨੂੰ ਘਟਾ ਸਕਦੀ ਹੈ।
ਨਿਯਮਤ ਨਿਰੀਖਣ:ਆਪਰੇਟਰਾਂ ਨੂੰ ਨੁਕਸਾਨ ਜਾਂ ਘਿਸਾਅ ਦੇ ਕਿਸੇ ਵੀ ਸੰਕੇਤ ਲਈ ਪੀਸਣ ਵਾਲੀ ਡਿਸਕ ਦੀ ਨਿਯਮਿਤ ਤੌਰ 'ਤੇ ਜਾਂਚ ਕਰਨੀ ਚਾਹੀਦੀ ਹੈ। ਇੱਕ ਖਾਸ ਬਿੰਦੂ ਤੋਂ ਵੱਧ ਘਿਸਾਅ ਦਿਖਾਉਣ ਵਾਲੀਆਂ ਡਿਸਕਾਂ ਨੂੰ ਤੁਰੰਤ ਬਦਲਿਆ ਜਾਣਾ ਚਾਹੀਦਾ ਹੈ।
ਡਿਸਕ ਦਾ ਆਕਾਰ ਅਤੇ RPM ਅਨੁਕੂਲਤਾ:
ਸਹੀ ਆਕਾਰ:ਗ੍ਰਾਈਂਡਰ ਲਈ ਸਹੀ ਡਿਸਕ ਆਕਾਰ ਦੀ ਵਰਤੋਂ ਕਰਨਾ ਬਹੁਤ ਜ਼ਰੂਰੀ ਹੈ। ਗਲਤ ਆਕਾਰ ਦੀਆਂ ਡਿਸਕਾਂ ਅਸਮਾਨ ਢੰਗ ਨਾਲ ਟੁੱਟ ਸਕਦੀਆਂ ਹਨ ਜਾਂ ਸੁਰੱਖਿਆ ਜੋਖਮ ਪੈਦਾ ਕਰ ਸਕਦੀਆਂ ਹਨ।
RPM ਅਨੁਕੂਲਤਾ:ਪੀਸਣ ਵਾਲੀ ਡਿਸਕ ਲਈ ਸਿਫ਼ਾਰਸ਼ ਕੀਤੇ ਗਏ ਘੁੰਮਣ ਪ੍ਰਤੀ ਮਿੰਟ (RPM) ਦੀ ਪਾਲਣਾ ਕਰਨ ਨਾਲ ਸਰਵੋਤਮ ਪ੍ਰਦਰਸ਼ਨ ਯਕੀਨੀ ਬਣਦਾ ਹੈ ਅਤੇ ਸਮੇਂ ਤੋਂ ਪਹਿਲਾਂ ਖਰਾਬ ਹੋਣ ਤੋਂ ਬਚਦਾ ਹੈ।
ਨਿਯਮਤ ਰੱਖ-ਰਖਾਅ, ਸਿਫ਼ਾਰਸ਼ ਕੀਤੀਆਂ ਓਪਰੇਟਿੰਗ ਹਾਲਤਾਂ ਦੀ ਪਾਲਣਾ, ਅਤੇ ਕੰਮ ਲਈ ਸਹੀ ਪੀਸਣ ਵਾਲੀ ਡਿਸਕ ਦੀ ਚੋਣ ਕਰਨਾ, ਟੁੱਟ-ਭੱਜ ਨੂੰ ਘੱਟ ਕਰਨ ਲਈ ਜ਼ਰੂਰੀ ਅਭਿਆਸ ਹਨ। ਟੁੱਟ-ਭੱਜ ਨੂੰ ਪ੍ਰਭਾਵਿਤ ਕਰਨ ਵਾਲੇ ਕਾਰਕਾਂ ਨੂੰ ਸਮਝ ਕੇ, ਆਪਰੇਟਰ ਪੀਸਣ ਵਾਲੀ ਡਿਸਕ ਦੀ ਲੰਬੀ ਉਮਰ ਅਤੇ ਕੁਸ਼ਲਤਾ ਨੂੰ ਵਧਾ ਸਕਦੇ ਹਨ, ਸੁਰੱਖਿਅਤ ਅਤੇ ਵਧੇਰੇ ਉਤਪਾਦਕ ਪੀਸਣ ਦੇ ਕਾਰਜਾਂ ਵਿੱਚ ਯੋਗਦਾਨ ਪਾ ਸਕਦੇ ਹਨ।
ਅਸਮਾਨ ਪੀਸਣਾ
ਅਸਮਾਨ ਪੀਸਣਾ ਉਸ ਸਥਿਤੀ ਨੂੰ ਦਰਸਾਉਂਦਾ ਹੈ ਜਿੱਥੇ ਸਤ੍ਹਾ ਨੂੰ ਜ਼ਮੀਨ 'ਤੇ ਪੀਸਿਆ ਜਾਣ ਨਾਲ ਇਕਸਾਰ ਅਤੇ ਨਿਰਵਿਘਨ ਸਮਾਪਤੀ ਨਹੀਂ ਹੁੰਦੀ। ਇਹ ਸਮੱਸਿਆ ਕਈ ਕਾਰਨਾਂ ਕਰਕੇ ਪੈਦਾ ਹੋ ਸਕਦੀ ਹੈ ਅਤੇ ਵਰਕਪੀਸ ਦੀ ਗੁਣਵੱਤਾ ਨੂੰ ਪ੍ਰਭਾਵਤ ਕਰ ਸਕਦੀ ਹੈ। ਇੱਥੇ ਅਸਮਾਨ ਪੀਸਣ ਵਿੱਚ ਯੋਗਦਾਨ ਪਾਉਣ ਵਾਲੇ ਆਮ ਕਾਰਕ ਅਤੇ ਸੰਭਾਵੀ ਹੱਲ ਹਨ:
ਗਲਤ ਪੀਸਣ ਵਾਲੇ ਪਹੀਏ ਦੀ ਚੋਣ:
ਹੱਲ:ਇਹ ਯਕੀਨੀ ਬਣਾਓ ਕਿ ਪੀਸਣ ਵਾਲਾ ਪਹੀਆ ਪੀਸਿਆ ਜਾ ਰਿਹਾ ਸਮੱਗਰੀ ਲਈ ਢੁਕਵਾਂ ਹੈ। ਵੱਖ-ਵੱਖ ਸਮੱਗਰੀਆਂ ਨੂੰ ਖਾਸ ਘਸਾਉਣ ਵਾਲੇ ਗੁਣਾਂ ਦੀ ਲੋੜ ਹੁੰਦੀ ਹੈ। ਐਪਲੀਕੇਸ਼ਨ ਲਈ ਸਹੀ ਪਹੀਏ ਦੀ ਕਿਸਮ, ਗਰਿੱਟ ਦਾ ਆਕਾਰ ਅਤੇ ਬੰਧਨ ਚੁਣੋ।
ਗਲਤ ਪਹੀਏ ਦੀ ਡਰੈਸਿੰਗ:
ਕਾਰਨ:ਇੱਕ ਪੀਸਣ ਵਾਲਾ ਪਹੀਆ ਜੋ ਸਹੀ ਢੰਗ ਨਾਲ ਤਿਆਰ ਨਹੀਂ ਕੀਤਾ ਗਿਆ ਹੈ, ਅਸਮਾਨ ਘਿਸਾਅ ਅਤੇ ਬੇਅਸਰ ਕੱਟਣ ਦਾ ਕਾਰਨ ਬਣ ਸਕਦਾ ਹੈ।
ਹੱਲ:ਪੀਸਣ ਵਾਲੇ ਪਹੀਏ ਨੂੰ ਨਿਯਮਿਤ ਤੌਰ 'ਤੇ ਇਸਦੀ ਸ਼ਕਲ ਬਣਾਈ ਰੱਖਣ ਲਈ ਪਹਿਨੋ ਅਤੇ ਕਿਸੇ ਵੀ ਜਮ੍ਹਾਂ ਹੋਏ ਮਲਬੇ ਨੂੰ ਹਟਾਓ। ਸਹੀ ਡਰੈਸਿੰਗ ਇੱਕ ਇਕਸਾਰ ਕੱਟਣ ਵਾਲੀ ਸਤਹ ਨੂੰ ਯਕੀਨੀ ਬਣਾਉਂਦੀ ਹੈ।
ਨਾਕਾਫ਼ੀ ਪੀਸਣ ਵਾਲਾ ਤਰਲ ਜਾਂ ਕੂਲੈਂਟ:
ਕਾਰਨ:ਪੀਸਣ ਵਾਲੇ ਤਰਲ ਦੀ ਨਾਕਾਫ਼ੀ ਜਾਂ ਗਲਤ ਵਰਤੋਂ ਦੇ ਨਤੀਜੇ ਵਜੋਂ ਰਗੜ ਅਤੇ ਗਰਮੀ ਵਧ ਸਕਦੀ ਹੈ, ਜਿਸ ਨਾਲ ਅਸਮਾਨ ਪੀਸਣਾ ਹੋ ਸਕਦਾ ਹੈ।
ਹੱਲ:ਗਰਮੀ ਨੂੰ ਦੂਰ ਕਰਨ ਅਤੇ ਰਗੜ ਘਟਾਉਣ ਲਈ ਇੱਕ ਢੁਕਵੇਂ ਪੀਸਣ ਵਾਲੇ ਤਰਲ ਜਾਂ ਕੂਲੈਂਟ ਦੀ ਵਰਤੋਂ ਕਰੋ। ਇਕਸਾਰ ਨਤੀਜੇ ਪ੍ਰਾਪਤ ਕਰਨ ਲਈ ਸਹੀ ਠੰਢਾ ਹੋਣਾ ਜ਼ਰੂਰੀ ਹੈ।
ਗਲਤ ਪੀਸਣ ਵਾਲੇ ਪੈਰਾਮੀਟਰ:
ਕਾਰਨ:ਗਲਤ ਪੀਸਣ ਦੇ ਮਾਪਦੰਡਾਂ ਜਿਵੇਂ ਕਿ ਬਹੁਤ ਜ਼ਿਆਦਾ ਗਤੀ, ਫੀਡ ਦਰ, ਜਾਂ ਕੱਟ ਦੀ ਡੂੰਘਾਈ ਦੀ ਵਰਤੋਂ ਕਰਨ ਨਾਲ ਅਸਮਾਨ ਪੀਸਣ ਹੋ ਸਕਦਾ ਹੈ।
ਹੱਲ:ਸਮੱਗਰੀ ਅਤੇ ਐਪਲੀਕੇਸ਼ਨ ਜ਼ਰੂਰਤਾਂ ਦੇ ਅਨੁਸਾਰ ਪੀਸਣ ਦੇ ਮਾਪਦੰਡਾਂ ਨੂੰ ਵਿਵਸਥਿਤ ਕਰੋ। ਅਨੁਕੂਲ ਸੈਟਿੰਗਾਂ ਲਈ ਨਿਰਮਾਤਾ ਦੀਆਂ ਸਿਫ਼ਾਰਸ਼ਾਂ ਵੇਖੋ।
ਘਿਸਿਆ ਹੋਇਆ ਪੀਸਣ ਵਾਲਾ ਪਹੀਆ:
ਕਾਰਨ:ਇੱਕ ਘਿਸਿਆ ਹੋਇਆ ਪੀਸਣ ਵਾਲਾ ਪਹੀਆ ਇੱਕਸਾਰ ਕੱਟਣ ਵਾਲੀ ਸਤ੍ਹਾ ਪ੍ਰਦਾਨ ਨਹੀਂ ਕਰ ਸਕਦਾ, ਜਿਸਦੇ ਨਤੀਜੇ ਵਜੋਂ ਅਸਮਾਨ ਪੀਸਣਾ ਹੁੰਦਾ ਹੈ।
ਹੱਲ:ਜਦੋਂ ਪੀਸਣ ਵਾਲਾ ਪਹੀਆ ਆਪਣੀ ਵਰਤੋਂ ਯੋਗ ਜ਼ਿੰਦਗੀ ਦੇ ਅੰਤ 'ਤੇ ਪਹੁੰਚ ਜਾਵੇ ਤਾਂ ਇਸਨੂੰ ਬਦਲ ਦਿਓ। ਪਹਿਨਣ ਦੇ ਸੰਕੇਤਾਂ ਲਈ ਪਹੀਏ ਦੀ ਨਿਯਮਿਤ ਤੌਰ 'ਤੇ ਜਾਂਚ ਕਰੋ।
ਅਸਮਾਨ ਦਬਾਅ ਜਾਂ ਫੀਡ ਦਰ:
ਕਾਰਨ:ਪੀਸਣ ਦੌਰਾਨ ਅਸਮਾਨ ਦਬਾਅ ਜਾਂ ਅਸੰਗਤ ਫੀਡ ਦਰਾਂ ਸਮੱਗਰੀ ਨੂੰ ਅਨਿਯਮਿਤ ਢੰਗ ਨਾਲ ਹਟਾਉਣ ਦਾ ਕਾਰਨ ਬਣ ਸਕਦੀਆਂ ਹਨ।
ਹੱਲ:ਵਰਕਪੀਸ 'ਤੇ ਇਕਸਾਰ ਦਬਾਅ ਲਾਗੂ ਕਰੋ ਅਤੇ ਇਕਸਾਰ ਫੀਡ ਰੇਟ ਬਣਾਈ ਰੱਖੋ। ਆਪਰੇਟਰ ਹੁਨਰ ਅਤੇ ਵੇਰਵਿਆਂ ਵੱਲ ਧਿਆਨ ਦੇਣਾ ਬਹੁਤ ਜ਼ਰੂਰੀ ਹੈ।
ਮਸ਼ੀਨ ਸੰਬੰਧੀ ਮੁੱਦੇ:
ਕਾਰਨ:ਪੀਸਣ ਵਾਲੀ ਮਸ਼ੀਨ ਨਾਲ ਮਕੈਨੀਕਲ ਸਮੱਸਿਆਵਾਂ, ਜਿਵੇਂ ਕਿ ਗਲਤ ਅਲਾਈਨਮੈਂਟ ਜਾਂ ਸਪਿੰਡਲ ਨਾਲ ਸਮੱਸਿਆਵਾਂ, ਅਸਮਾਨ ਪੀਸਣ ਦਾ ਕਾਰਨ ਬਣ ਸਕਦੀਆਂ ਹਨ।
ਹੱਲ:ਪੀਸਣ ਵਾਲੀ ਮਸ਼ੀਨ ਦੀ ਨਿਯਮਤ ਰੱਖ-ਰਖਾਅ ਜਾਂਚ ਕਰੋ। ਸਹੀ ਕਾਰਜਸ਼ੀਲਤਾ ਨੂੰ ਯਕੀਨੀ ਬਣਾਉਣ ਲਈ ਕਿਸੇ ਵੀ ਮਕੈਨੀਕਲ ਸਮੱਸਿਆ ਨੂੰ ਤੁਰੰਤ ਹੱਲ ਕਰੋ।
ਵਰਕਪੀਸ ਫਿਕਸਿੰਗ:
ਕਾਰਨ:ਮਾੜੀ ਤਰ੍ਹਾਂ ਸੁਰੱਖਿਅਤ ਜਾਂ ਗਲਤ ਢੰਗ ਨਾਲ ਬਣਾਏ ਗਏ ਵਰਕਪੀਸ ਅਸਮਾਨ ਪੀਸਣ ਦਾ ਕਾਰਨ ਬਣ ਸਕਦੇ ਹਨ।
ਹੱਲ:ਵਰਕਪੀਸ ਦੀ ਸਹੀ ਫਿਕਸਚਰਿੰਗ ਅਤੇ ਅਲਾਈਨਮੈਂਟ ਯਕੀਨੀ ਬਣਾਓ। ਪੀਸਣ ਦੀ ਪ੍ਰਕਿਰਿਆ ਦੌਰਾਨ ਹਿੱਲਜੁਲ ਨੂੰ ਰੋਕਣ ਲਈ ਇਸਨੂੰ ਮਜ਼ਬੂਤੀ ਨਾਲ ਸੁਰੱਖਿਅਤ ਕਰੋ।
ਅਸਮਾਨ ਪੀਸਣ ਨੂੰ ਹੱਲ ਕਰਨ ਲਈ ਸਹੀ ਉਪਕਰਣ ਸੈੱਟਅੱਪ, ਸਹੀ ਓਪਰੇਟਿੰਗ ਮਾਪਦੰਡਾਂ ਅਤੇ ਨਿਯਮਤ ਰੱਖ-ਰਖਾਅ ਅਭਿਆਸਾਂ ਦੇ ਸੁਮੇਲ ਦੀ ਲੋੜ ਹੁੰਦੀ ਹੈ। ਪੀਸਣ ਦੇ ਕਾਰਜਾਂ ਵਿੱਚ ਉੱਚ-ਗੁਣਵੱਤਾ ਅਤੇ ਇਕਸਾਰ ਨਤੀਜੇ ਪ੍ਰਾਪਤ ਕਰਨ ਲਈ ਆਪਰੇਟਰਾਂ ਨੂੰ ਤੁਰੰਤ ਮੁੱਦਿਆਂ ਦੀ ਪਛਾਣ ਕਰਨ ਅਤੇ ਉਹਨਾਂ ਨੂੰ ਠੀਕ ਕਰਨ ਲਈ ਸਿਖਲਾਈ ਦਿੱਤੀ ਜਾਣੀ ਚਾਹੀਦੀ ਹੈ। ਨਿਯਮਤ ਨਿਰੀਖਣ ਅਤੇ ਵਧੀਆ ਅਭਿਆਸਾਂ ਦੀ ਪਾਲਣਾ ਪੀਸਣ ਦੀ ਪ੍ਰਕਿਰਿਆ ਦੌਰਾਨ ਕੁਸ਼ਲ ਅਤੇ ਇਕਸਾਰ ਸਮੱਗਰੀ ਨੂੰ ਹਟਾਉਣ ਵਿੱਚ ਯੋਗਦਾਨ ਪਾਉਂਦੀ ਹੈ।
ਜ਼ਿਆਦਾ ਗਰਮ ਹੋਣ ਦੀਆਂ ਸਮੱਸਿਆਵਾਂ
ਪੀਸਣ ਦੌਰਾਨ ਜ਼ਿਆਦਾ ਗਰਮ ਹੋਣਾ ਇੱਕ ਆਮ ਸਮੱਸਿਆ ਹੈ ਜੋ ਪੀਸਣ ਵਾਲੇ ਪਹੀਏ ਅਤੇ ਵਰਕਪੀਸ ਦੋਵਾਂ ਦੀ ਕਾਰਗੁਜ਼ਾਰੀ ਨੂੰ ਪ੍ਰਭਾਵਿਤ ਕਰ ਸਕਦੀ ਹੈ। ਬਹੁਤ ਜ਼ਿਆਦਾ ਗਰਮੀ ਕਈ ਸਮੱਸਿਆਵਾਂ ਦਾ ਕਾਰਨ ਬਣ ਸਕਦੀ ਹੈ, ਜਿਸ ਵਿੱਚ ਪਹੀਏ ਦੀ ਉਮਰ ਘੱਟਣਾ, ਵਰਕਪੀਸ ਨੂੰ ਥਰਮਲ ਨੁਕਸਾਨ, ਅਤੇ ਸਮੁੱਚੀ ਘੱਟ ਪੀਸਣ ਦੀ ਕੁਸ਼ਲਤਾ ਸ਼ਾਮਲ ਹੈ। ਓਵਰਹੀਟਿੰਗ ਸਮੱਸਿਆਵਾਂ ਨੂੰ ਹੱਲ ਕਰਨ ਲਈ ਇੱਥੇ ਸੰਭਾਵੀ ਕਾਰਨ ਅਤੇ ਹੱਲ ਹਨ:
ਗਲਤ ਪੀਸਣ ਵਾਲੇ ਪੈਰਾਮੀਟਰ:
ਕਾਰਨ:ਗਲਤ ਪੀਸਣ ਵਾਲੇ ਮਾਪਦੰਡਾਂ ਦੀ ਵਰਤੋਂ, ਜਿਵੇਂ ਕਿ ਬਹੁਤ ਜ਼ਿਆਦਾ ਗਤੀ, ਫੀਡ ਦਰ, ਜਾਂ ਕੱਟ ਦੀ ਡੂੰਘਾਈ, ਵਾਧੂ ਗਰਮੀ ਪੈਦਾ ਕਰ ਸਕਦੀ ਹੈ।
ਹੱਲ:ਪੀਸਣ ਦੇ ਮਾਪਦੰਡਾਂ ਨੂੰ ਸਿਫ਼ਾਰਸ਼ ਕੀਤੀ ਸੀਮਾ ਦੇ ਅੰਦਰ ਵਿਵਸਥਿਤ ਕਰੋ। ਪੀਸਿਆ ਜਾ ਰਿਹਾ ਸਮੱਗਰੀ ਦੇ ਆਧਾਰ 'ਤੇ ਅਨੁਕੂਲ ਸੈਟਿੰਗਾਂ ਲਈ ਨਿਰਮਾਤਾ ਦੇ ਦਿਸ਼ਾ-ਨਿਰਦੇਸ਼ਾਂ ਦੀ ਸਲਾਹ ਲਓ।
ਨਾਕਾਫ਼ੀ ਕੂਲਿੰਗ ਜਾਂ ਲੁਬਰੀਕੇਸ਼ਨ:
ਕਾਰਨ:ਕੂਲੈਂਟ ਜਾਂ ਪੀਸਣ ਵਾਲੇ ਤਰਲ ਦੀ ਨਾਕਾਫ਼ੀ ਵਰਤੋਂ ਦੇ ਨਤੀਜੇ ਵਜੋਂ ਰਗੜ ਅਤੇ ਗਰਮੀ ਵਧ ਸਕਦੀ ਹੈ।
ਹੱਲ:ਪੀਸਣ ਦੀ ਪ੍ਰਕਿਰਿਆ ਦੌਰਾਨ ਕੂਲੈਂਟ ਜਾਂ ਲੁਬਰੀਕੈਂਟ ਦੀ ਢੁਕਵੀਂ ਸਪਲਾਈ ਯਕੀਨੀ ਬਣਾਓ। ਸਹੀ ਠੰਢਾ ਹੋਣ ਨਾਲ ਗਰਮੀ ਦੂਰ ਹੁੰਦੀ ਹੈ ਅਤੇ ਥਰਮਲ ਨੁਕਸਾਨ ਨੂੰ ਰੋਕਿਆ ਜਾਂਦਾ ਹੈ।
ਗਲਤ ਪਹੀਏ ਦੀ ਚੋਣ:
ਕਾਰਨ:ਪੀਸਣ ਵਾਲੀ ਸਮੱਗਰੀ ਲਈ ਅਣਉਚਿਤ ਵਿਸ਼ੇਸ਼ਤਾਵਾਂ ਵਾਲਾ ਪੀਸਣ ਵਾਲਾ ਪਹੀਆ ਚੁਣਨ ਨਾਲ ਜ਼ਿਆਦਾ ਗਰਮੀ ਹੋ ਸਕਦੀ ਹੈ।
ਹੱਲ:ਖਾਸ ਵਰਤੋਂ ਲਈ ਸਹੀ ਘਸਾਉਣ ਵਾਲੀ ਕਿਸਮ, ਗਰਿੱਟ ਦੇ ਆਕਾਰ ਅਤੇ ਬਾਂਡ ਵਾਲਾ ਪੀਸਣ ਵਾਲਾ ਪਹੀਆ ਚੁਣੋ। ਪਹੀਏ ਨੂੰ ਸਮੱਗਰੀ ਨਾਲ ਮਿਲਾਉਣ ਨਾਲ ਗਰਮੀ ਪੈਦਾ ਹੋਣ ਨੂੰ ਘੱਟ ਤੋਂ ਘੱਟ ਕੀਤਾ ਜਾਂਦਾ ਹੈ।
ਵਰਕਪੀਸ ਸਮੱਗਰੀ ਦੇ ਮੁੱਦੇ:
ਕਾਰਨ:ਕੁਝ ਸਮੱਗਰੀਆਂ, ਖਾਸ ਕਰਕੇ ਜਿਨ੍ਹਾਂ ਦੀ ਥਰਮਲ ਚਾਲਕਤਾ ਘੱਟ ਹੁੰਦੀ ਹੈ, ਪੀਸਣ ਦੌਰਾਨ ਜ਼ਿਆਦਾ ਗਰਮ ਹੋਣ ਦਾ ਖ਼ਤਰਾ ਵਧੇਰੇ ਹੁੰਦਾ ਹੈ।
ਹੱਲ:ਘੱਟ ਥਰਮਲ ਚਾਲਕਤਾ ਵਾਲੀਆਂ ਸਮੱਗਰੀਆਂ ਲਈ ਪੀਸਣ ਦੇ ਮਾਪਦੰਡਾਂ ਨੂੰ ਵਿਵਸਥਿਤ ਕਰੋ। ਗਰਮੀ-ਸੰਵੇਦਨਸ਼ੀਲ ਸਮੱਗਰੀਆਂ ਲਈ ਤਿਆਰ ਕੀਤੇ ਗਏ ਇੱਕ ਵਿਸ਼ੇਸ਼ ਪੀਸਣ ਵਾਲੇ ਪਹੀਏ ਦੀ ਵਰਤੋਂ ਕਰਨ 'ਤੇ ਵਿਚਾਰ ਕਰੋ।
ਪਹੀਏ ਦੀ ਡਰੈਸਿੰਗ ਦੀਆਂ ਸਮੱਸਿਆਵਾਂ:
ਕਾਰਨ:ਪੀਸਣ ਵਾਲੇ ਪਹੀਏ ਦੀ ਅਨਿਯਮਿਤਤਾ ਜਾਂ ਗਲਤ ਡ੍ਰੈਸਿੰਗ ਅਸਮਾਨ ਸੰਪਰਕ ਅਤੇ ਗਰਮੀ ਦੇ ਨਿਰਮਾਣ ਦਾ ਕਾਰਨ ਬਣ ਸਕਦੀ ਹੈ।
ਹੱਲ:ਪੀਸਣ ਵਾਲੇ ਪਹੀਏ ਨੂੰ ਨਿਯਮਿਤ ਤੌਰ 'ਤੇ ਤਿਆਰ ਕਰੋ ਤਾਂ ਜੋ ਇਸਦੀ ਸ਼ਕਲ ਬਣਾਈ ਰੱਖੀ ਜਾ ਸਕੇ ਅਤੇ ਕਿਸੇ ਵੀ ਗਲੇਜ਼ਿੰਗ ਜਾਂ ਜਮ੍ਹਾਂ ਹੋਏ ਮਲਬੇ ਨੂੰ ਹਟਾਇਆ ਜਾ ਸਕੇ। ਸਹੀ ਢੰਗ ਨਾਲ ਤਿਆਰ ਕੀਤੇ ਪਹੀਏ ਇਕਸਾਰ ਪੀਸਣ ਦੀ ਕਾਰਗੁਜ਼ਾਰੀ ਨੂੰ ਯਕੀਨੀ ਬਣਾਉਂਦੇ ਹਨ।
ਮਸ਼ੀਨ ਦੀ ਨਾਕਾਫ਼ੀ ਦੇਖਭਾਲ:
ਕਾਰਨ:ਮਾੜੀ ਦੇਖਭਾਲ ਵਾਲੀਆਂ ਪੀਸਣ ਵਾਲੀਆਂ ਮਸ਼ੀਨਾਂ ਓਵਰਹੀਟਿੰਗ ਦੀਆਂ ਸਮੱਸਿਆਵਾਂ ਵਿੱਚ ਯੋਗਦਾਨ ਪਾ ਸਕਦੀਆਂ ਹਨ।
ਹੱਲ:ਪੀਸਣ ਵਾਲੀ ਮਸ਼ੀਨ ਦੀ ਨਿਯਮਤ ਦੇਖਭਾਲ ਕਰੋ, ਜਿਸ ਵਿੱਚ ਕੂਲੈਂਟ ਸਿਸਟਮ ਦੀ ਜਾਂਚ ਕਰਨਾ, ਵ੍ਹੀਲ ਡ੍ਰੈਸਿੰਗ ਉਪਕਰਣਾਂ ਦੀ ਜਾਂਚ ਕਰਨਾ, ਅਤੇ ਸਹੀ ਅਲਾਈਨਮੈਂਟ ਨੂੰ ਯਕੀਨੀ ਬਣਾਉਣਾ ਸ਼ਾਮਲ ਹੈ। ਕਿਸੇ ਵੀ ਮਕੈਨੀਕਲ ਸਮੱਸਿਆ ਨੂੰ ਤੁਰੰਤ ਹੱਲ ਕਰੋ।
ਨਾਕਾਫ਼ੀ ਪਹੀਏ ਦਾ ਕੂਲੈਂਟ ਪ੍ਰਵਾਹ:
ਕਾਰਨ:ਪੀਸਣ ਵਾਲੇ ਜ਼ੋਨ ਵਿੱਚ ਕੂਲੈਂਟ ਦਾ ਨਾਕਾਫ਼ੀ ਪ੍ਰਵਾਹ ਗਰਮੀ ਦੇ ਨਿਕਾਸ ਨੂੰ ਘਟਾ ਸਕਦਾ ਹੈ।
ਹੱਲ:ਕੂਲੈਂਟ ਡਿਲੀਵਰੀ ਸਿਸਟਮ ਦੀ ਜਾਂਚ ਕਰੋ ਅਤੇ ਅਨੁਕੂਲ ਬਣਾਓ। ਇਹ ਯਕੀਨੀ ਬਣਾਓ ਕਿ ਕੂਲੈਂਟ ਕੂਲਿੰਗ ਕੁਸ਼ਲਤਾ ਬਣਾਈ ਰੱਖਣ ਲਈ ਪੀਸਣ ਵਾਲੇ ਜ਼ੋਨ ਤੱਕ ਪ੍ਰਭਾਵਸ਼ਾਲੀ ਢੰਗ ਨਾਲ ਪਹੁੰਚਦਾ ਹੈ।
ਬਹੁਤ ਜ਼ਿਆਦਾ ਪੀਸਣ ਦਾ ਸਮਾਂ:
ਕਾਰਨ:ਬਿਨਾਂ ਬ੍ਰੇਕ ਦੇ ਲੰਬੇ ਸਮੇਂ ਤੱਕ ਪੀਸਣ ਦੇ ਸੈਸ਼ਨ ਗਰਮੀ ਦੇ ਨਿਰਮਾਣ ਵਿੱਚ ਯੋਗਦਾਨ ਪਾ ਸਕਦੇ ਹਨ।
ਹੱਲ:ਰੁਕ-ਰੁਕ ਕੇ ਪੀਸਣਾ ਲਾਗੂ ਕਰੋ ਅਤੇ ਬਹੁਤ ਜ਼ਿਆਦਾ ਗਰਮੀ ਇਕੱਠੀ ਹੋਣ ਤੋਂ ਰੋਕਣ ਲਈ ਬ੍ਰੇਕ ਦਿਓ। ਇਹ ਤਰੀਕਾ ਖਾਸ ਤੌਰ 'ਤੇ ਵੱਡੇ ਜਾਂ ਚੁਣੌਤੀਪੂਰਨ ਪੀਸਣ ਵਾਲੇ ਕੰਮਾਂ ਲਈ ਮਹੱਤਵਪੂਰਨ ਹੈ।
ਪੀਸਣ ਵਿੱਚ ਓਵਰਹੀਟਿੰਗ ਸਮੱਸਿਆਵਾਂ ਨੂੰ ਹੱਲ ਕਰਨ ਲਈ ਇੱਕ ਵਿਆਪਕ ਪਹੁੰਚ ਦੀ ਲੋੜ ਹੁੰਦੀ ਹੈ ਜਿਸ ਵਿੱਚ ਸਹੀ ਉਪਕਰਣ ਸੈੱਟਅੱਪ, ਢੁਕਵੇਂ ਪੀਸਣ ਵਾਲੇ ਮਾਪਦੰਡ, ਅਤੇ ਨਿਯਮਤ ਰੱਖ-ਰਖਾਅ ਅਭਿਆਸ ਸ਼ਾਮਲ ਹੁੰਦੇ ਹਨ। ਆਪਰੇਟਰਾਂ ਨੂੰ ਪੀਸਣ ਦੀ ਪ੍ਰਕਿਰਿਆ ਦੌਰਾਨ ਗਰਮੀ ਪੈਦਾ ਕਰਨ ਦੀ ਨਿਗਰਾਨੀ ਅਤੇ ਨਿਯੰਤਰਣ ਕਰਨਾ ਚਾਹੀਦਾ ਹੈ ਤਾਂ ਜੋ ਅਨੁਕੂਲ ਪ੍ਰਦਰਸ਼ਨ, ਵਧੇ ਹੋਏ ਟੂਲ ਲਾਈਫ ਅਤੇ ਉੱਚ-ਗੁਣਵੱਤਾ ਵਾਲੇ ਨਤੀਜੇ ਯਕੀਨੀ ਬਣਾਏ ਜਾ ਸਕਣ।
ਵਾਈਬ੍ਰੇਸ਼ਨ ਚਿੰਤਾਵਾਂ
ਪੀਸਣ ਦੇ ਕੰਮ ਦੌਰਾਨ ਬਹੁਤ ਜ਼ਿਆਦਾ ਵਾਈਬ੍ਰੇਸ਼ਨ ਕਈ ਤਰ੍ਹਾਂ ਦੀਆਂ ਸਮੱਸਿਆਵਾਂ ਦਾ ਕਾਰਨ ਬਣ ਸਕਦੀ ਹੈ, ਜਿਸ ਵਿੱਚ ਸਤ੍ਹਾ ਦੀ ਗੁਣਵੱਤਾ ਵਿੱਚ ਕਮੀ, ਔਜ਼ਾਰਾਂ ਦੇ ਘਿਸਾਅ ਵਿੱਚ ਵਾਧਾ, ਅਤੇ ਪੀਸਣ ਵਾਲੀ ਮਸ਼ੀਨ ਨੂੰ ਸੰਭਾਵੀ ਨੁਕਸਾਨ ਸ਼ਾਮਲ ਹੈ। ਸਟੀਕ ਅਤੇ ਕੁਸ਼ਲ ਪੀਸਣ ਦੀਆਂ ਪ੍ਰਕਿਰਿਆਵਾਂ ਨੂੰ ਪ੍ਰਾਪਤ ਕਰਨ ਲਈ ਵਾਈਬ੍ਰੇਸ਼ਨ ਸੰਬੰਧੀ ਚਿੰਤਾਵਾਂ ਨੂੰ ਹੱਲ ਕਰਨਾ ਬਹੁਤ ਜ਼ਰੂਰੀ ਹੈ। ਵਾਈਬ੍ਰੇਸ਼ਨ ਸਮੱਸਿਆਵਾਂ ਨੂੰ ਘਟਾਉਣ ਲਈ ਇੱਥੇ ਸੰਭਾਵੀ ਕਾਰਨ ਅਤੇ ਹੱਲ ਹਨ:
ਅਸਮਾਨ ਪਹੀਏ ਦਾ ਵਿਅਰ:
ਕਾਰਨ:ਪੀਸਣ ਵਾਲੇ ਪਹੀਏ 'ਤੇ ਅਨਿਯਮਿਤ ਘਿਸਾਅ ਦੇ ਨਤੀਜੇ ਵਜੋਂ ਵਰਕਪੀਸ ਨਾਲ ਅਸਮਾਨ ਸੰਪਰਕ ਹੋ ਸਕਦਾ ਹੈ, ਜਿਸ ਨਾਲ ਵਾਈਬ੍ਰੇਸ਼ਨ ਹੋ ਸਕਦੀ ਹੈ।
ਹੱਲ:ਇੱਕਸਾਰ ਅਤੇ ਸਮਤਲ ਸਤ੍ਹਾ ਬਣਾਈ ਰੱਖਣ ਲਈ ਪੀਸਣ ਵਾਲੇ ਪਹੀਏ ਦੀ ਨਿਯਮਿਤ ਤੌਰ 'ਤੇ ਜਾਂਚ ਕਰੋ ਅਤੇ ਕੱਪੜੇ ਪਾਓ। ਪਹੀਏ ਦੀ ਸਹੀ ਦੇਖਭਾਲ ਵਾਈਬ੍ਰੇਸ਼ਨ ਨੂੰ ਘੱਟ ਕਰਨ ਵਿੱਚ ਮਦਦ ਕਰਦੀ ਹੈ।
ਅਸੰਤੁਲਿਤ ਪੀਸਣ ਵਾਲਾ ਪਹੀਆ:
ਕਾਰਨ:ਪੀਸਣ ਵਾਲੇ ਪਹੀਏ ਵਿੱਚ ਅਸੰਤੁਲਨ, ਭਾਵੇਂ ਅਸਮਾਨ ਪਹਿਨਣ ਜਾਂ ਨਿਰਮਾਣ ਨੁਕਸ ਕਾਰਨ, ਵਾਈਬ੍ਰੇਸ਼ਨ ਦਾ ਕਾਰਨ ਬਣ ਸਕਦਾ ਹੈ।
ਹੱਲ:ਵ੍ਹੀਲ ਬੈਲੇਂਸਰ ਦੀ ਵਰਤੋਂ ਕਰਕੇ ਪੀਸਣ ਵਾਲੇ ਪਹੀਏ ਨੂੰ ਸੰਤੁਲਿਤ ਕਰੋ। ਸੰਤੁਲਨ ਭਾਰ ਦੀ ਬਰਾਬਰ ਵੰਡ ਨੂੰ ਯਕੀਨੀ ਬਣਾਉਂਦਾ ਹੈ ਅਤੇ ਓਪਰੇਸ਼ਨ ਦੌਰਾਨ ਵਾਈਬ੍ਰੇਸ਼ਨ ਘਟਾਉਂਦਾ ਹੈ।
ਮਸ਼ੀਨ ਕੈਲੀਬ੍ਰੇਸ਼ਨ ਦੀ ਘਾਟ:
ਕਾਰਨ:ਮਸ਼ੀਨ ਦੇ ਹਿੱਸਿਆਂ, ਜਿਵੇਂ ਕਿ ਵ੍ਹੀਲ ਸਪਿੰਡਲ ਜਾਂ ਵਰਕਟੇਬਲ, ਦੀ ਮਾੜੀ ਕੈਲੀਬ੍ਰੇਸ਼ਨ ਜਾਂ ਗਲਤ ਅਲਾਈਨਮੈਂਟ, ਵਾਈਬ੍ਰੇਸ਼ਨ ਵਿੱਚ ਯੋਗਦਾਨ ਪਾ ਸਕਦੀ ਹੈ।
ਹੱਲ:ਸਹੀ ਕਾਰਜਸ਼ੀਲਤਾ ਨੂੰ ਯਕੀਨੀ ਬਣਾਉਣ ਲਈ ਨਿਯਮਿਤ ਤੌਰ 'ਤੇ ਮਸ਼ੀਨ ਦੇ ਹਿੱਸਿਆਂ ਨੂੰ ਕੈਲੀਬਰੇਟ ਅਤੇ ਇਕਸਾਰ ਕਰੋ। ਮਸ਼ੀਨ ਸੈੱਟਅੱਪ ਅਤੇ ਇਕਸਾਰਤਾ ਲਈ ਨਿਰਮਾਤਾ ਦੇ ਦਿਸ਼ਾ-ਨਿਰਦੇਸ਼ਾਂ ਦੀ ਪਾਲਣਾ ਕਰੋ।
ਵਰਕਪੀਸ ਅਸੰਤੁਲਨ:
ਕਾਰਨ:ਇੱਕ ਅਸਮਾਨ ਜਾਂ ਗਲਤ ਢੰਗ ਨਾਲ ਸੁਰੱਖਿਅਤ ਵਰਕਪੀਸ ਅਸੰਤੁਲਨ ਪੈਦਾ ਕਰ ਸਕਦਾ ਹੈ ਅਤੇ ਵਾਈਬ੍ਰੇਸ਼ਨ ਪੈਦਾ ਕਰ ਸਕਦਾ ਹੈ।
ਹੱਲ:ਵਰਕਪੀਸ ਨੂੰ ਸਹੀ ਢੰਗ ਨਾਲ ਸੁਰੱਖਿਅਤ ਕਰੋ, ਇਹ ਯਕੀਨੀ ਬਣਾਉਂਦੇ ਹੋਏ ਕਿ ਇਹ ਬਰਾਬਰ ਸਥਿਤੀ ਵਿੱਚ ਹੈ ਅਤੇ ਕਲੈਂਪ ਕੀਤਾ ਗਿਆ ਹੈ। ਪੀਸਣ ਦੀ ਪ੍ਰਕਿਰਿਆ ਸ਼ੁਰੂ ਕਰਨ ਤੋਂ ਪਹਿਲਾਂ ਕਿਸੇ ਵੀ ਅਸੰਤੁਲਨ ਦੇ ਮੁੱਦੇ ਨੂੰ ਹੱਲ ਕਰੋ।
ਗਲਤ ਪਹੀਏ ਦੀ ਚੋਣ:
ਕਾਰਨ:ਅਣਉਚਿਤ ਵਿਸ਼ੇਸ਼ਤਾਵਾਂ ਵਾਲੇ ਪੀਸਣ ਵਾਲੇ ਪਹੀਏ ਦੀ ਵਰਤੋਂ ਕਰਨ ਨਾਲ ਵਾਈਬ੍ਰੇਸ਼ਨ ਹੋ ਸਕਦੀ ਹੈ।
ਹੱਲ:ਪੀਸਣ ਵਾਲੀ ਸਮੱਗਰੀ ਲਈ ਸਹੀ ਘਸਾਉਣ ਵਾਲੀ ਕਿਸਮ, ਗਰਿੱਟ ਦੇ ਆਕਾਰ ਅਤੇ ਬੰਧਨ ਵਾਲਾ ਪੀਸਣ ਵਾਲਾ ਪਹੀਆ ਚੁਣੋ। ਪਹੀਏ ਨੂੰ ਐਪਲੀਕੇਸ਼ਨ ਨਾਲ ਮੇਲਣ ਨਾਲ ਵਾਈਬ੍ਰੇਸ਼ਨ ਘੱਟ ਹੁੰਦੀ ਹੈ।
ਮਸ਼ੀਨ ਦਾ ਟੁੱਟਣਾ ਅਤੇ ਫਟਣਾ:
ਕਾਰਨ:ਮਸ਼ੀਨ ਦੇ ਖਰਾਬ ਜਾਂ ਖਰਾਬ ਹੋਏ ਹਿੱਸੇ, ਜਿਵੇਂ ਕਿ ਬੇਅਰਿੰਗ ਜਾਂ ਸਪਿੰਡਲ, ਵਾਈਬ੍ਰੇਸ਼ਨ ਵਿੱਚ ਯੋਗਦਾਨ ਪਾ ਸਕਦੇ ਹਨ।
ਹੱਲ:ਮਸ਼ੀਨ ਦੇ ਖਰਾਬ ਪੁਰਜ਼ਿਆਂ ਦੀ ਨਿਯਮਤ ਤੌਰ 'ਤੇ ਜਾਂਚ ਕਰੋ ਅਤੇ ਬਦਲੋ। ਸਹੀ ਰੱਖ-ਰਖਾਅ ਬਹੁਤ ਜ਼ਿਆਦਾ ਵਾਈਬ੍ਰੇਸ਼ਨਾਂ ਨੂੰ ਰੋਕਣ ਵਿੱਚ ਮਦਦ ਕਰਦਾ ਹੈ ਅਤੇ ਪੀਸਣ ਵਾਲੀ ਮਸ਼ੀਨ ਦੀ ਉਮਰ ਵਧਾਉਂਦਾ ਹੈ।
ਨਾਕਾਫ਼ੀ ਕੂਲੈਂਟ ਪ੍ਰਵਾਹ:
ਕਾਰਨ:ਪੀਸਣ ਵਾਲੇ ਖੇਤਰ ਵਿੱਚ ਕੂਲੈਂਟ ਦਾ ਨਾਕਾਫ਼ੀ ਪ੍ਰਵਾਹ ਗਰਮੀ ਦੇ ਨਿਰਮਾਣ ਅਤੇ ਵਾਈਬ੍ਰੇਸ਼ਨ ਦਾ ਕਾਰਨ ਬਣ ਸਕਦਾ ਹੈ।
ਹੱਲ:ਸਹੀ ਕੂਲਿੰਗ ਨੂੰ ਯਕੀਨੀ ਬਣਾਉਣ ਲਈ ਕੂਲੈਂਟ ਡਿਲੀਵਰੀ ਸਿਸਟਮ ਨੂੰ ਅਨੁਕੂਲ ਬਣਾਓ। ਪ੍ਰਭਾਵਸ਼ਾਲੀ ਕੂਲਿੰਗ ਥਰਮਲ ਫੈਲਾਅ ਅਤੇ ਸੁੰਗੜਨ ਦੇ ਜੋਖਮ ਨੂੰ ਘਟਾਉਂਦੀ ਹੈ, ਜਿਸ ਨਾਲ ਵਾਈਬ੍ਰੇਸ਼ਨ ਹੋ ਸਕਦੀ ਹੈ।
ਟੂਲ ਹੋਲਡਰ ਮੁੱਦੇ:
ਕਾਰਨ:ਟੂਲ ਹੋਲਡਰ ਜਾਂ ਸਪਿੰਡਲ ਇੰਟਰਫੇਸ ਨਾਲ ਸਮੱਸਿਆਵਾਂ ਵਾਈਬ੍ਰੇਸ਼ਨਾਂ ਪੈਦਾ ਕਰ ਸਕਦੀਆਂ ਹਨ।
ਹੱਲ:ਯਕੀਨੀ ਬਣਾਓ ਕਿ ਟੂਲ ਹੋਲਡਰ ਸੁਰੱਖਿਅਤ ਢੰਗ ਨਾਲ ਮਾਊਂਟ ਕੀਤਾ ਗਿਆ ਹੈ ਅਤੇ ਸਪਿੰਡਲ ਨਾਲ ਸਹੀ ਢੰਗ ਨਾਲ ਇਕਸਾਰ ਹੈ। ਵਾਈਬ੍ਰੇਸ਼ਨਾਂ ਨੂੰ ਘੱਟ ਤੋਂ ਘੱਟ ਕਰਨ ਲਈ ਉੱਚ-ਗੁਣਵੱਤਾ ਵਾਲੇ ਅਤੇ ਸਹੀ ਢੰਗ ਨਾਲ ਰੱਖ-ਰਖਾਅ ਵਾਲੇ ਟੂਲ ਹੋਲਡਰਾਂ ਦੀ ਵਰਤੋਂ ਕਰੋ।
ਮਸ਼ੀਨ ਫਾਊਂਡੇਸ਼ਨ:
ਕਾਰਨ:ਮਸ਼ੀਨ ਦੀ ਮਾੜੀ ਨੀਂਹ ਜਾਂ ਨਾਕਾਫ਼ੀ ਸਹਾਰਾ ਵਾਈਬ੍ਰੇਸ਼ਨ ਨੂੰ ਵਧਾ ਸਕਦਾ ਹੈ।
ਹੱਲ:ਇਹ ਯਕੀਨੀ ਬਣਾਓ ਕਿ ਪੀਸਣ ਵਾਲੀ ਮਸ਼ੀਨ ਇੱਕ ਸਥਿਰ ਅਤੇ ਸਹੀ ਢੰਗ ਨਾਲ ਡਿਜ਼ਾਈਨ ਕੀਤੀ ਗਈ ਨੀਂਹ 'ਤੇ ਸਥਾਪਿਤ ਕੀਤੀ ਗਈ ਹੈ। ਮਸ਼ੀਨ ਵਿੱਚ ਸੰਚਾਰਿਤ ਵਾਈਬ੍ਰੇਸ਼ਨਾਂ ਨੂੰ ਘੱਟ ਤੋਂ ਘੱਟ ਕਰਨ ਲਈ ਕਿਸੇ ਵੀ ਢਾਂਚਾਗਤ ਮੁੱਦੇ ਨੂੰ ਹੱਲ ਕਰੋ।
ਪੀਸਣ ਵਿੱਚ ਵਾਈਬ੍ਰੇਸ਼ਨ ਸੰਬੰਧੀ ਚਿੰਤਾਵਾਂ ਨੂੰ ਪ੍ਰਭਾਵਸ਼ਾਲੀ ਢੰਗ ਨਾਲ ਹੱਲ ਕਰਨ ਲਈ ਸਹੀ ਮਸ਼ੀਨ ਰੱਖ-ਰਖਾਅ, ਪਹੀਏ ਦੀ ਚੋਣ, ਅਤੇ ਵਰਕਪੀਸ ਹੈਂਡਲਿੰਗ ਦੇ ਸੁਮੇਲ ਦੀ ਲੋੜ ਹੁੰਦੀ ਹੈ। ਆਪਰੇਟਰਾਂ ਨੂੰ ਸਮੱਸਿਆਵਾਂ ਦੀ ਤੁਰੰਤ ਪਛਾਣ ਕਰਨ ਅਤੇ ਹੱਲ ਕਰਨ ਲਈ ਨਿਯਮਤ ਨਿਰੀਖਣ ਅਤੇ ਰੱਖ-ਰਖਾਅ ਅਭਿਆਸਾਂ ਨੂੰ ਲਾਗੂ ਕਰਨਾ ਚਾਹੀਦਾ ਹੈ, ਜਿਸਦੇ ਨਤੀਜੇ ਵਜੋਂ ਪੀਸਣ ਦੀ ਕਾਰਗੁਜ਼ਾਰੀ ਅਤੇ ਗੁਣਵੱਤਾ ਵਿੱਚ ਸੁਧਾਰ ਹੁੰਦਾ ਹੈ।
ਪੀਸਣ ਵਿੱਚ ਲੋਡਿੰਗ ਸਮੱਸਿਆਵਾਂ
ਪੀਸਣ ਵਿੱਚ ਲੋਡਿੰਗ ਉਸ ਵਰਤਾਰੇ ਨੂੰ ਦਰਸਾਉਂਦੀ ਹੈ ਜਿੱਥੇ ਪੀਸਣ ਵਾਲੇ ਪਹੀਏ 'ਤੇ ਘਸਾਉਣ ਵਾਲੇ ਦਾਣਿਆਂ ਦੇ ਵਿਚਕਾਰ ਖਾਲੀ ਥਾਂ ਜ਼ਮੀਨ 'ਤੇ ਹੋਣ ਵਾਲੀ ਸਮੱਗਰੀ ਨਾਲ ਭਰ ਜਾਂਦੀ ਹੈ, ਜਿਸਦੇ ਨਤੀਜੇ ਵਜੋਂ ਕੱਟਣ ਦੀ ਕਿਰਿਆ ਘੱਟ ਜਾਂਦੀ ਹੈ ਅਤੇ ਰਗੜ ਵਧ ਜਾਂਦੀ ਹੈ। ਲੋਡਿੰਗ ਪੀਸਣ ਦੀ ਪ੍ਰਕਿਰਿਆ ਦੀ ਕੁਸ਼ਲਤਾ ਅਤੇ ਗੁਣਵੱਤਾ 'ਤੇ ਨਕਾਰਾਤਮਕ ਪ੍ਰਭਾਵ ਪਾ ਸਕਦੀ ਹੈ। ਲੋਡਿੰਗ ਸਮੱਸਿਆਵਾਂ ਨੂੰ ਹੱਲ ਕਰਨ ਲਈ ਇੱਥੇ ਸੰਭਾਵੀ ਕਾਰਨ ਅਤੇ ਹੱਲ ਹਨ:
ਸਾਫਟ ਵਰਕਪੀਸ ਸਮੱਗਰੀ:
ਕਾਰਨ:ਨਰਮ ਸਮੱਗਰੀ ਨੂੰ ਪੀਸਣ ਨਾਲ ਘਿਸਣ ਵਾਲੇ ਦਾਣੇ ਤੇਜ਼ੀ ਨਾਲ ਬੰਦ ਹੋ ਸਕਦੇ ਹਨ।
ਹੱਲ:ਨਰਮ ਸਮੱਗਰੀ 'ਤੇ ਕੰਮ ਕਰਦੇ ਸਮੇਂ ਮੋਟੇ ਗਰਿੱਟ ਅਤੇ ਖੁੱਲ੍ਹੇ ਢਾਂਚੇ ਵਾਲੇ ਪੀਸਣ ਵਾਲੇ ਪਹੀਏ ਦੀ ਵਰਤੋਂ ਕਰੋ। ਇਹ ਤੇਜ਼ ਲੋਡਿੰਗ ਨੂੰ ਰੋਕਣ ਵਿੱਚ ਮਦਦ ਕਰਦਾ ਹੈ ਅਤੇ ਚਿੱਪ ਨੂੰ ਕੁਸ਼ਲਤਾ ਨਾਲ ਹਟਾਉਣ ਦੀ ਆਗਿਆ ਦਿੰਦਾ ਹੈ।
ਪਦਾਰਥ ਦੀ ਦੂਸ਼ਿਤਤਾ:
ਕਾਰਨ:ਵਰਕਪੀਸ ਸਮੱਗਰੀ ਵਿੱਚ ਮੌਜੂਦ ਦੂਸ਼ਿਤ ਪਦਾਰਥ, ਜਿਵੇਂ ਕਿ ਤੇਲ, ਗਰੀਸ, ਜਾਂ ਕੂਲੈਂਟ ਰਹਿੰਦ-ਖੂੰਹਦ, ਲੋਡਿੰਗ ਵਿੱਚ ਯੋਗਦਾਨ ਪਾ ਸਕਦੇ ਹਨ।
ਹੱਲ:ਗੰਦਗੀ ਨੂੰ ਹਟਾਉਣ ਲਈ ਪੀਸਣ ਤੋਂ ਪਹਿਲਾਂ ਵਰਕਪੀਸ ਦੀ ਸਹੀ ਸਫਾਈ ਯਕੀਨੀ ਬਣਾਓ। ਲੋਡਿੰਗ ਨੂੰ ਘੱਟ ਤੋਂ ਘੱਟ ਕਰਨ ਲਈ ਢੁਕਵੇਂ ਕੱਟਣ ਵਾਲੇ ਤਰਲ ਪਦਾਰਥਾਂ ਜਾਂ ਕੂਲੈਂਟਾਂ ਦੀ ਵਰਤੋਂ ਕਰੋ।
ਗਲਤ ਕੂਲੈਂਟ ਐਪਲੀਕੇਸ਼ਨ:
ਕਾਰਨ:ਕੂਲੈਂਟ ਦੀ ਨਾਕਾਫ਼ੀ ਜਾਂ ਗਲਤ ਵਰਤੋਂ ਨਾਲ ਲੁਬਰੀਕੇਸ਼ਨ ਅਤੇ ਕੂਲਿੰਗ ਦੀ ਘਾਟ ਹੋ ਸਕਦੀ ਹੈ, ਜਿਸਦੇ ਨਤੀਜੇ ਵਜੋਂ ਲੋਡਿੰਗ ਹੋ ਸਕਦੀ ਹੈ।
ਹੱਲ:ਕੂਲੈਂਟ ਦੇ ਪ੍ਰਵਾਹ ਅਤੇ ਗਾੜ੍ਹਾਪਣ ਨੂੰ ਅਨੁਕੂਲ ਬਣਾਓ। ਇਹ ਯਕੀਨੀ ਬਣਾਓ ਕਿ ਕੂਲੈਂਟ ਪ੍ਰਕਿਰਿਆ ਨੂੰ ਲੁਬਰੀਕੇਟ ਅਤੇ ਠੰਡਾ ਕਰਨ ਲਈ ਪੀਸਣ ਵਾਲੇ ਜ਼ੋਨ ਤੱਕ ਪ੍ਰਭਾਵਸ਼ਾਲੀ ਢੰਗ ਨਾਲ ਪਹੁੰਚਦਾ ਹੈ, ਲੋਡਿੰਗ ਨੂੰ ਰੋਕਦਾ ਹੈ।
ਪਹੀਏ ਦੀ ਨਾਕਾਫ਼ੀ ਤਿੱਖਾਪਨ:
ਕਾਰਨ:ਸੁਸਤ ਜਾਂ ਘਿਸੇ ਹੋਏ ਪੀਸਣ ਵਾਲੇ ਪਹੀਏ ਲੋਡ ਹੋਣ ਦਾ ਜ਼ਿਆਦਾ ਖ਼ਤਰਾ ਰੱਖਦੇ ਹਨ ਕਿਉਂਕਿ ਉਹ ਆਪਣੀ ਕੱਟਣ ਦੀ ਕੁਸ਼ਲਤਾ ਗੁਆ ਦਿੰਦੇ ਹਨ।
ਹੱਲ:ਪੀਸਣ ਵਾਲੇ ਪਹੀਏ ਦੀ ਤਿੱਖਾਪਨ ਬਣਾਈ ਰੱਖਣ ਲਈ ਇਸਨੂੰ ਨਿਯਮਿਤ ਤੌਰ 'ਤੇ ਤਿਆਰ ਕਰੋ ਅਤੇ ਤਿੱਖਾ ਕਰੋ। ਤਾਜ਼ੇ ਘਸਾਉਣ ਵਾਲੇ ਦਾਣਿਆਂ ਨੂੰ ਬਾਹਰ ਕੱਢਣ ਅਤੇ ਕੱਟਣ ਦੀ ਕਿਰਿਆ ਨੂੰ ਵਧਾਉਣ ਲਈ ਵ੍ਹੀਲ ਡ੍ਰੈਸਰ ਦੀ ਵਰਤੋਂ ਕਰੋ।
ਘੱਟ ਪਹੀਏ ਦੀ ਗਤੀ:
ਕਾਰਨ:ਪੀਸਣ ਵਾਲੇ ਪਹੀਏ ਨੂੰ ਘੱਟ ਗਤੀ 'ਤੇ ਚਲਾਉਣ ਨਾਲ ਚਿਪਸ ਨੂੰ ਬਾਹਰ ਕੱਢਣ ਲਈ ਕਾਫ਼ੀ ਸੈਂਟਰਿਫਿਊਗਲ ਬਲ ਨਹੀਂ ਮਿਲ ਸਕਦਾ, ਜਿਸ ਕਾਰਨ ਲੋਡਿੰਗ ਹੋ ਸਕਦੀ ਹੈ।
ਹੱਲ:ਇਹ ਯਕੀਨੀ ਬਣਾਓ ਕਿ ਪੀਸਣ ਵਾਲੀ ਮਸ਼ੀਨ ਖਾਸ ਪਹੀਏ ਅਤੇ ਵਰਕਪੀਸ ਦੇ ਸੁਮੇਲ ਲਈ ਸਿਫ਼ਾਰਸ਼ ਕੀਤੀ ਗਤੀ 'ਤੇ ਕੰਮ ਕਰਦੀ ਹੈ। ਉੱਚ ਗਤੀ ਚਿੱਪ ਨੂੰ ਬਿਹਤਰ ਢੰਗ ਨਾਲ ਹਟਾਉਣ ਵਿੱਚ ਮਦਦ ਕਰ ਸਕਦੀ ਹੈ।
ਬਹੁਤ ਜ਼ਿਆਦਾ ਦਬਾਅ:
ਕਾਰਨ:ਪੀਸਣ ਦੌਰਾਨ ਬਹੁਤ ਜ਼ਿਆਦਾ ਦਬਾਅ ਪਾਉਣ ਨਾਲ ਸਮੱਗਰੀ ਪਹੀਏ ਵਿੱਚ ਧੱਕੀ ਜਾ ਸਕਦੀ ਹੈ, ਜਿਸ ਨਾਲ ਲੋਡਿੰਗ ਹੋ ਸਕਦੀ ਹੈ।
ਹੱਲ:ਦਰਮਿਆਨੇ ਅਤੇ ਇਕਸਾਰ ਪੀਸਣ ਵਾਲੇ ਦਬਾਅ ਦੀ ਵਰਤੋਂ ਕਰੋ। ਫੀਡ ਰੇਟ ਨੂੰ ਐਡਜਸਟ ਕਰੋ ਤਾਂ ਜੋ ਪਹੀਏ ਨੂੰ ਬਿਨਾਂ ਕਿਸੇ ਜ਼ਿਆਦਾ ਦਬਾਅ ਦੇ ਕੁਸ਼ਲਤਾ ਨਾਲ ਕੱਟਣ ਦਿੱਤਾ ਜਾ ਸਕੇ ਜਿਸ ਨਾਲ ਲੋਡਿੰਗ ਹੁੰਦੀ ਹੈ।
ਗਲਤ ਪਹੀਏ ਦੇ ਨਿਰਧਾਰਨ:
ਕਾਰਨ:ਪੀਸਣ ਵਾਲੇ ਪਹੀਏ ਦੀ ਵਰਤੋਂ ਜਿਸ ਵਿੱਚ ਸਮੱਗਰੀ ਨੂੰ ਪੀਸਿਆ ਜਾ ਰਿਹਾ ਹੈ, ਗਲਤ ਵਿਸ਼ੇਸ਼ਤਾਵਾਂ ਹੋਣ ਕਰਕੇ ਲੋਡਿੰਗ ਹੋ ਸਕਦੀ ਹੈ।
ਹੱਲ:ਖਾਸ ਐਪਲੀਕੇਸ਼ਨ ਲਈ ਢੁਕਵੀਂ ਘਸਾਉਣ ਵਾਲੀ ਕਿਸਮ, ਗਰਿੱਟ ਦੇ ਆਕਾਰ ਅਤੇ ਬਾਂਡ ਵਾਲਾ ਪੀਸਣ ਵਾਲਾ ਪਹੀਆ ਚੁਣੋ। ਪਹੀਏ ਨੂੰ ਸਮੱਗਰੀ ਨਾਲ ਮੇਲਣ ਨਾਲ ਲੋਡਿੰਗ ਨੂੰ ਰੋਕਣ ਵਿੱਚ ਮਦਦ ਮਿਲਦੀ ਹੈ।
ਕੂਲੈਂਟ ਦੀ ਨਾਕਾਫ਼ੀ ਸਫਾਈ:
ਕਾਰਨ:ਦੂਸ਼ਿਤ ਜਾਂ ਪੁਰਾਣਾ ਕੂਲੈਂਟ ਲੋਡਿੰਗ ਸਮੱਸਿਆਵਾਂ ਵਿੱਚ ਯੋਗਦਾਨ ਪਾ ਸਕਦਾ ਹੈ।
ਹੱਲ:ਕੂਲੈਂਟ ਨੂੰ ਨਿਯਮਿਤ ਤੌਰ 'ਤੇ ਸਾਫ਼ ਕਰੋ ਅਤੇ ਬਦਲੋ ਤਾਂ ਜੋ ਗੰਦਗੀ ਦੇ ਜਮ੍ਹਾਂ ਹੋਣ ਤੋਂ ਬਚਿਆ ਜਾ ਸਕੇ। ਤਾਜ਼ਾ ਅਤੇ ਸਾਫ਼ ਕੂਲੈਂਟ ਲੁਬਰੀਕੇਸ਼ਨ ਅਤੇ ਕੂਲਿੰਗ ਨੂੰ ਵਧਾਉਂਦਾ ਹੈ, ਜਿਸ ਨਾਲ ਲੋਡਿੰਗ ਦੀ ਸੰਭਾਵਨਾ ਘੱਟ ਜਾਂਦੀ ਹੈ।
ਗਲਤ ਡਰੈਸਿੰਗ ਤਕਨੀਕ:
ਕਾਰਨ:ਪੀਸਣ ਵਾਲੇ ਪਹੀਏ ਦੀ ਗਲਤ ਡ੍ਰੈਸਿੰਗ ਬੇਨਿਯਮੀਆਂ ਅਤੇ ਲੋਡਿੰਗ ਦਾ ਕਾਰਨ ਬਣ ਸਕਦੀ ਹੈ।
ਹੱਲ:ਢੁਕਵੇਂ ਡ੍ਰੈਸਿੰਗ ਟੂਲ ਦੀ ਵਰਤੋਂ ਕਰਕੇ ਪਹੀਏ ਨੂੰ ਸਹੀ ਢੰਗ ਨਾਲ ਸਜਾਓ। ਇਹ ਯਕੀਨੀ ਬਣਾਓ ਕਿ ਪਹੀਏ ਦਾ ਪ੍ਰੋਫਾਈਲ ਇਕਸਾਰ ਹੋਵੇ ਅਤੇ ਲੋਡਿੰਗ ਨੂੰ ਰੋਕਣ ਲਈ ਬੇਨਿਯਮੀਆਂ ਤੋਂ ਮੁਕਤ ਹੋਵੇ।
ਲੋਡਿੰਗ ਮੁੱਦਿਆਂ ਨੂੰ ਪ੍ਰਭਾਵਸ਼ਾਲੀ ਢੰਗ ਨਾਲ ਹੱਲ ਕਰਨ ਲਈ ਸਹੀ ਪਹੀਏ ਦੀ ਚੋਣ, ਮਸ਼ੀਨ ਸੈੱਟਅੱਪ, ਅਤੇ ਰੱਖ-ਰਖਾਅ ਅਭਿਆਸਾਂ ਦਾ ਸੁਮੇਲ ਸ਼ਾਮਲ ਹੈ। ਆਪਰੇਟਰਾਂ ਨੂੰ ਸਿਫ਼ਾਰਸ਼ ਕੀਤੀਆਂ ਪ੍ਰਕਿਰਿਆਵਾਂ ਦੀ ਪਾਲਣਾ ਕਰਨੀ ਚਾਹੀਦੀ ਹੈ, ਢੁਕਵੇਂ ਪੀਸਣ ਵਾਲੇ ਮਾਪਦੰਡਾਂ ਦੀ ਵਰਤੋਂ ਕਰਨੀ ਚਾਹੀਦੀ ਹੈ, ਅਤੇ ਲੋਡਿੰਗ ਨੂੰ ਘੱਟ ਤੋਂ ਘੱਟ ਕਰਨ ਅਤੇ ਪੀਸਣ ਦੀ ਕਾਰਗੁਜ਼ਾਰੀ ਨੂੰ ਅਨੁਕੂਲ ਬਣਾਉਣ ਲਈ ਨਿਯਮਤ ਪਹੀਏ ਦੀ ਡ੍ਰੈਸਿੰਗ ਲਾਗੂ ਕਰਨੀ ਚਾਹੀਦੀ ਹੈ।
ਵੱਖ-ਵੱਖ ਧਾਤੂ ਕਾਰਜਾਂ ਅਤੇ ਨਿਰਮਾਣ ਕਾਰਜਾਂ ਵਿੱਚ ਅਨੁਕੂਲ ਨਤੀਜੇ ਪ੍ਰਾਪਤ ਕਰਨ ਲਈ ਸਹੀ ਪੀਸਣ ਵਾਲੀ ਡਿਸਕ ਦੀ ਚੋਣ ਕਰਨਾ ਬਹੁਤ ਜ਼ਰੂਰੀ ਹੈ। ਚੋਣ ਕਾਰਕਾਂ 'ਤੇ ਨਿਰਭਰ ਕਰਦੀ ਹੈ ਜਿਵੇਂ ਕਿ ਕੰਮ ਕੀਤੀ ਜਾ ਰਹੀ ਸਮੱਗਰੀ, ਲੋੜੀਂਦੀ ਫਿਨਿਸ਼, ਅਤੇ ਵਰਤੀ ਜਾ ਰਹੀ ਗ੍ਰਾਈਂਡਰ ਦੀ ਕਿਸਮ।
ਸਹੀ ਪੀਸਣ ਵਾਲੀ ਡਿਸਕ ਦੀ ਚੋਣ ਕਰਨਾ
ਸਮੱਗਰੀ ਅਨੁਕੂਲਤਾ:
ਲੋਹ ਧਾਤਾਂ (ਸਟੀਲ, ਲੋਹਾ):ਖਾਸ ਤੌਰ 'ਤੇ ਫੈਰਸ ਧਾਤਾਂ ਲਈ ਤਿਆਰ ਕੀਤੀਆਂ ਗਈਆਂ ਪੀਸਣ ਵਾਲੀਆਂ ਡਿਸਕਾਂ ਦੀ ਵਰਤੋਂ ਕਰੋ। ਇਹਨਾਂ ਡਿਸਕਾਂ ਵਿੱਚ ਅਕਸਰ ਸਟੀਲ ਦੀ ਕਠੋਰਤਾ ਲਈ ਢੁਕਵੇਂ ਘਸਾਉਣ ਵਾਲੇ ਪਦਾਰਥ ਹੁੰਦੇ ਹਨ ਅਤੇ ਇਹਨਾਂ 'ਤੇ ਲੋਡਿੰਗ ਘੱਟ ਹੁੰਦੀ ਹੈ।
ਗੈਰ-ਫੈਰਸ ਧਾਤਾਂ (ਐਲੂਮੀਨੀਅਮ, ਪਿੱਤਲ):ਨਰਮ ਧਾਤਾਂ ਲਈ ਢੁਕਵੇਂ ਘਸਾਉਣ ਵਾਲੇ ਡਿਸਕ ਚੁਣੋ ਤਾਂ ਜੋ ਜੰਮਣ ਤੋਂ ਬਚਿਆ ਜਾ ਸਕੇ। ਐਲੂਮੀਨੀਅਮ ਆਕਸਾਈਡ ਜਾਂ ਸਿਲੀਕਾਨ ਕਾਰਬਾਈਡ ਡਿਸਕ ਆਮ ਵਿਕਲਪ ਹਨ।
ਘਸਾਉਣ ਵਾਲੀ ਸਮੱਗਰੀ:
ਐਲੂਮੀਨੀਅਮ ਆਕਸਾਈਡ:ਫੈਰਸ ਧਾਤਾਂ 'ਤੇ ਆਮ-ਉਦੇਸ਼ ਪੀਸਣ ਲਈ ਢੁਕਵਾਂ। ਇਹ ਟਿਕਾਊ ਅਤੇ ਬਹੁਪੱਖੀ ਹੈ।
ਜ਼ਿਰਕੋਨੀਆ ਐਲੂਮਿਨਾ:ਉੱਚ ਕੱਟਣ ਕੁਸ਼ਲਤਾ ਅਤੇ ਲੰਬੀ ਉਮਰ ਦੀ ਪੇਸ਼ਕਸ਼ ਕਰਦਾ ਹੈ, ਜੋ ਇਸਨੂੰ ਫੈਰਸ ਅਤੇ ਗੈਰ-ਫੈਰਸ ਧਾਤਾਂ 'ਤੇ ਹਮਲਾਵਰ ਪੀਸਣ ਲਈ ਢੁਕਵਾਂ ਬਣਾਉਂਦਾ ਹੈ।
ਸਿਲੀਕਾਨ ਕਾਰਬਾਈਡ:ਗੈਰ-ਫੈਰਸ ਧਾਤਾਂ ਅਤੇ ਪੱਥਰ ਨੂੰ ਪੀਸਣ ਲਈ ਆਦਰਸ਼। ਇਹ ਅਲਮੀਨੀਅਮ ਆਕਸਾਈਡ ਨਾਲੋਂ ਤਿੱਖਾ ਹੈ ਪਰ ਘੱਟ ਟਿਕਾਊ ਹੈ।
ਗਰਿੱਟ ਦਾ ਆਕਾਰ:
ਮੋਟਾ ਗਰਿੱਟ (24-36):ਤੇਜ਼ੀ ਨਾਲ ਸਟਾਕ ਹਟਾਉਣਾ ਅਤੇ ਭਾਰੀ-ਡਿਊਟੀ ਪੀਸਣਾ।
ਦਰਮਿਆਨਾ ਗਰਿੱਟ (40-60):ਸਟਾਕ ਹਟਾਉਣ ਅਤੇ ਸਤ੍ਹਾ ਦੀ ਸਮਾਪਤੀ ਨੂੰ ਸੰਤੁਲਿਤ ਕਰਦਾ ਹੈ।
ਬਰੀਕ ਗਰਿੱਟ (80-120):ਇੱਕ ਨਿਰਵਿਘਨ ਫਿਨਿਸ਼ ਪ੍ਰਦਾਨ ਕਰਦਾ ਹੈ, ਜੋ ਸਤ੍ਹਾ ਦੀ ਤਿਆਰੀ ਅਤੇ ਹਲਕੇ ਪੀਸਣ ਲਈ ਢੁਕਵਾਂ ਹੈ।
ਪਹੀਏ ਦੀ ਕਿਸਮ:
ਕਿਸਮ 27 (ਉਦਾਸੀ ਕੇਂਦਰ):ਸਮਤਲ ਸਤ੍ਹਾ ਵਾਲੀ ਸਟੈਂਡਰਡ ਪੀਸਣ ਵਾਲੀ ਡਿਸਕ, ਸਤ੍ਹਾ ਪੀਸਣ ਅਤੇ ਕਿਨਾਰੇ ਦੇ ਕੰਮ ਲਈ ਆਦਰਸ਼।
ਕਿਸਮ 29 (ਕੋਨਿਕਲ):ਹਮਲਾਵਰ ਸਟਾਕ ਹਟਾਉਣ ਅਤੇ ਬਿਹਤਰ ਸਤਹ ਮਿਸ਼ਰਣ ਲਈ ਕੋਣ ਵਾਲਾ ਡਿਜ਼ਾਈਨ।
ਕਿਸਮ 1 (ਸਿੱਧਾ):ਕੱਟ-ਆਫ ਐਪਲੀਕੇਸ਼ਨਾਂ ਲਈ ਵਰਤਿਆ ਜਾਂਦਾ ਹੈ। ਇਹ ਸਹੀ ਕੱਟਣ ਲਈ ਇੱਕ ਪਤਲਾ ਪ੍ਰੋਫਾਈਲ ਪ੍ਰਦਾਨ ਕਰਦਾ ਹੈ।
ਐਪਲੀਕੇਸ਼ਨ:
ਪੀਸਣਾ:ਸਮੱਗਰੀ ਨੂੰ ਹਟਾਉਣ ਅਤੇ ਆਕਾਰ ਦੇਣ ਲਈ ਮਿਆਰੀ ਪੀਸਣ ਵਾਲੀਆਂ ਡਿਸਕਾਂ।
ਕੱਟਣਾ:ਧਾਤ ਨੂੰ ਕੱਟਣ ਲਈ ਕੱਟੇ ਹੋਏ ਪਹੀਏ ਵਰਤੋ, ਜੋ ਕਿ ਸਿੱਧਾ ਅਤੇ ਸਾਫ਼ ਕਿਨਾਰਾ ਪ੍ਰਦਾਨ ਕਰਦੇ ਹਨ।
ਫਲੈਪ ਡਿਸਕ:ਪੀਸਣ ਅਤੇ ਫਿਨਿਸ਼ਿੰਗ ਨੂੰ ਇੱਕ ਵਿੱਚ ਮਿਲਾਓ। ਸਤਹਾਂ ਨੂੰ ਮਿਲਾਉਣ ਅਤੇ ਸਮੂਥ ਕਰਨ ਲਈ ਢੁਕਵਾਂ।
ਗ੍ਰਾਈਂਡਰ ਨਾਲ ਅਨੁਕੂਲਤਾ:
ਇਹ ਯਕੀਨੀ ਬਣਾਓ ਕਿ ਪੀਸਣ ਵਾਲੀ ਡਿਸਕ ਵਰਤੀ ਜਾ ਰਹੀ ਗ੍ਰਾਈਂਡਰ ਦੀ ਕਿਸਮ ਅਤੇ ਗਤੀ ਦੇ ਅਨੁਕੂਲ ਹੈ। ਡਿਸਕ ਦੇ ਵੱਧ ਤੋਂ ਵੱਧ RPM (ਰਿਵੋਲਿਊਸ਼ਨ ਪ੍ਰਤੀ ਮਿੰਟ) ਲਈ ਨਿਰਮਾਤਾ ਦੀਆਂ ਸਿਫ਼ਾਰਸ਼ਾਂ ਦੀ ਜਾਂਚ ਕਰੋ।
ਕਾਰਜ ਵਿਸ਼ੇਸ਼ਤਾ:
ਭਾਰੀ ਸਟਾਕ ਹਟਾਉਣਾ:ਕੁਸ਼ਲ ਸਮੱਗਰੀ ਹਟਾਉਣ ਲਈ ਇੱਕ ਮੋਟਾ ਗਰਿੱਟ ਅਤੇ ਇੱਕ ਟਾਈਪ 27 ਜਾਂ ਟਾਈਪ 29 ਡਿਸਕ ਚੁਣੋ।
ਸਤ੍ਹਾ ਫਿਨਿਸ਼ਿੰਗ:ਨਿਰਵਿਘਨ ਫਿਨਿਸ਼ ਲਈ ਫਲੈਪ ਡਿਸਕਾਂ ਵਾਲੇ ਦਰਮਿਆਨੇ ਤੋਂ ਬਰੀਕ ਗਰਿੱਟਸ ਦੀ ਚੋਣ ਕਰੋ।
ਸੁਰੱਖਿਆ ਦੇ ਵਿਚਾਰ:
ਸੁਰੱਖਿਆ ਦਿਸ਼ਾ-ਨਿਰਦੇਸ਼ਾਂ ਦੀ ਪਾਲਣਾ ਕਰੋ, ਜਿਸ ਵਿੱਚ ਸੁਰੱਖਿਆ ਗਲਾਸ ਅਤੇ ਦਸਤਾਨੇ ਵਰਗੇ ਢੁਕਵੇਂ ਨਿੱਜੀ ਸੁਰੱਖਿਆ ਉਪਕਰਣ (PPE) ਪਹਿਨਣਾ ਸ਼ਾਮਲ ਹੈ।
ਵਾਧੂ ਟਿਕਾਊਤਾ ਅਤੇ ਸੁਰੱਖਿਆ ਲਈ ਮਜ਼ਬੂਤ ਡਿਸਕਾਂ ਦੀ ਚੋਣ ਕਰੋ।
ਬ੍ਰਾਂਡ ਅਤੇ ਗੁਣਵੱਤਾ:
ਗੁਣਵੱਤਾ ਅਤੇ ਇਕਸਾਰਤਾ ਲਈ ਜਾਣੇ ਜਾਂਦੇ ਨਾਮਵਰ ਬ੍ਰਾਂਡਾਂ ਤੋਂ ਡਿਸਕਾਂ ਦੀ ਚੋਣ ਕਰੋ। ਉੱਚ-ਗੁਣਵੱਤਾ ਵਾਲੀਆਂ ਡਿਸਕਾਂ ਬਿਹਤਰ ਪ੍ਰਦਰਸ਼ਨ ਅਤੇ ਟਿਕਾਊਤਾ ਦੀ ਪੇਸ਼ਕਸ਼ ਕਰਦੀਆਂ ਹਨ।
ਲਾਗਤ 'ਤੇ ਵਿਚਾਰ:
ਸ਼ੁਰੂਆਤੀ ਲਾਗਤ ਨੂੰ ਪੀਸਣ ਵਾਲੀ ਡਿਸਕ ਦੀ ਸੰਭਾਵਿਤ ਉਮਰ ਅਤੇ ਪ੍ਰਦਰਸ਼ਨ ਨਾਲ ਸੰਤੁਲਿਤ ਕਰੋ। ਉੱਚ-ਗੁਣਵੱਤਾ ਵਾਲੀਆਂ ਡਿਸਕਾਂ ਦੀ ਸ਼ੁਰੂਆਤੀ ਲਾਗਤ ਵੱਧ ਹੋ ਸਕਦੀ ਹੈ ਪਰ ਸਮੇਂ ਦੇ ਨਾਲ ਬਿਹਤਰ ਮੁੱਲ ਪ੍ਰਦਾਨ ਕਰ ਸਕਦੀ ਹੈ।
ਇਹਨਾਂ ਕਾਰਕਾਂ 'ਤੇ ਵਿਚਾਰ ਕਰਕੇ, ਆਪਰੇਟਰ ਆਪਣੇ ਖਾਸ ਐਪਲੀਕੇਸ਼ਨਾਂ ਲਈ ਸਹੀ ਪੀਸਣ ਵਾਲੀ ਡਿਸਕ ਦੀ ਚੋਣ ਕਰ ਸਕਦੇ ਹਨ, ਕੁਸ਼ਲਤਾ, ਸੁਰੱਖਿਆ ਅਤੇ ਅਨੁਕੂਲ ਨਤੀਜਿਆਂ ਨੂੰ ਯਕੀਨੀ ਬਣਾਉਂਦੇ ਹੋਏ।
ਸਿੱਟਾ
ਸਿੱਟੇ ਵਜੋਂ, ਢੁਕਵੀਂ ਪੀਸਣ ਵਾਲੀ ਡਿਸਕ ਦੀ ਚੋਣ ਕਰਨਾ ਸਫਲ ਧਾਤੂ ਕਾਰਜ ਅਤੇ ਨਿਰਮਾਣ ਨਤੀਜਿਆਂ ਨੂੰ ਪ੍ਰਾਪਤ ਕਰਨ ਦਾ ਇੱਕ ਮਹੱਤਵਪੂਰਨ ਪਹਿਲੂ ਹੈ। ਚੋਣ ਵੱਖ-ਵੱਖ ਕਾਰਕਾਂ 'ਤੇ ਨਿਰਭਰ ਕਰਦੀ ਹੈ ਜਿਵੇਂ ਕਿ ਕੰਮ ਕੀਤੀ ਜਾ ਰਹੀ ਸਮੱਗਰੀ, ਲੋੜੀਂਦੀ ਫਿਨਿਸ਼, ਅਤੇ ਵਰਤੋਂ ਵਿੱਚ ਪੀਸਣ ਵਾਲੀ ਕਿਸਮ। ਸਮੱਗਰੀ ਦੀ ਅਨੁਕੂਲਤਾ, ਘਸਾਉਣ ਵਾਲੀ ਕਿਸਮ, ਗਰਿੱਟ ਦਾ ਆਕਾਰ, ਪਹੀਏ ਦੀ ਕਿਸਮ, ਐਪਲੀਕੇਸ਼ਨ, ਗ੍ਰਾਈਂਡਰ ਅਨੁਕੂਲਤਾ, ਕਾਰਜ ਵਿਸ਼ੇਸ਼ਤਾ, ਸੁਰੱਖਿਆ, ਬ੍ਰਾਂਡ ਗੁਣਵੱਤਾ ਅਤੇ ਲਾਗਤ 'ਤੇ ਵਿਚਾਰ ਕਰਕੇ, ਆਪਰੇਟਰ ਆਪਣੀਆਂ ਪੀਸਣ ਦੀਆਂ ਪ੍ਰਕਿਰਿਆਵਾਂ ਵਿੱਚ ਕੁਸ਼ਲਤਾ ਅਤੇ ਸੁਰੱਖਿਆ ਨੂੰ ਵਧਾਉਣ ਲਈ ਸੂਚਿਤ ਫੈਸਲੇ ਲੈ ਸਕਦੇ ਹਨ।
ਸੁਰੱਖਿਆ ਦਿਸ਼ਾ-ਨਿਰਦੇਸ਼ਾਂ ਦੀ ਪਾਲਣਾ ਕਰਨਾ, ਢੁਕਵੇਂ ਨਿੱਜੀ ਸੁਰੱਖਿਆ ਉਪਕਰਣ ਪਹਿਨਣਾ, ਅਤੇ ਗ੍ਰਾਈਂਡਰ ਅਤੇ ਡਿਸਕ ਅਨੁਕੂਲਤਾ ਲਈ ਨਿਰਮਾਤਾ ਦੀਆਂ ਸਿਫ਼ਾਰਸ਼ਾਂ ਦੀ ਪਾਲਣਾ ਕਰਨਾ ਜ਼ਰੂਰੀ ਹੈ। ਭਾਵੇਂ ਇਹ ਭਾਰੀ ਸਟਾਕ ਹਟਾਉਣ, ਸਤ੍ਹਾ ਨੂੰ ਫਿਨਿਸ਼ ਕਰਨ, ਜਾਂ ਕੱਟਣ ਦੀਆਂ ਐਪਲੀਕੇਸ਼ਨਾਂ ਲਈ ਹੋਵੇ, ਸਹੀ ਗ੍ਰਾਈਂਡਰ ਡਿਸਕ ਕੰਮ ਦੀ ਗੁਣਵੱਤਾ ਅਤੇ ਕੁਸ਼ਲਤਾ ਨੂੰ ਮਹੱਤਵਪੂਰਨ ਤੌਰ 'ਤੇ ਪ੍ਰਭਾਵਤ ਕਰ ਸਕਦੀ ਹੈ।
ਇਸ ਤੋਂ ਇਲਾਵਾ, ਘਿਸਾਅ ਅਤੇ ਅੱਥਰੂ ਲਈ ਸਮੇਂ-ਸਮੇਂ 'ਤੇ ਜਾਂਚ, ਓਵਰਹੀਟਿੰਗ ਅਤੇ ਵਾਈਬ੍ਰੇਸ਼ਨ ਸੰਬੰਧੀ ਚਿੰਤਾਵਾਂ ਵਰਗੇ ਮੁੱਦਿਆਂ ਨੂੰ ਹੱਲ ਕਰਨਾ, ਅਤੇ ਲੋਡਿੰਗ ਸਮੱਸਿਆਵਾਂ ਨੂੰ ਸਮਝਣਾ ਗ੍ਰਾਈਂਡਿੰਗ ਡਿਸਕ ਦੇ ਜੀਵਨ ਨੂੰ ਲੰਮਾ ਕਰਨ ਅਤੇ ਇਕਸਾਰ ਪ੍ਰਦਰਸ਼ਨ ਨੂੰ ਯਕੀਨੀ ਬਣਾਉਣ ਵਿੱਚ ਯੋਗਦਾਨ ਪਾਉਂਦਾ ਹੈ।
ਸੰਖੇਪ ਵਿੱਚ, ਪੀਸਣ ਵਾਲੀਆਂ ਡਿਸਕਾਂ ਦੀ ਚੋਣ, ਵਰਤੋਂ ਅਤੇ ਰੱਖ-ਰਖਾਅ ਲਈ ਇੱਕ ਚੰਗੀ ਤਰ੍ਹਾਂ ਸੂਚਿਤ ਅਤੇ ਯੋਜਨਾਬੱਧ ਪਹੁੰਚ ਅਨੁਕੂਲ ਨਤੀਜੇ ਪ੍ਰਾਪਤ ਕਰਨ, ਉਤਪਾਦਕਤਾ ਵਧਾਉਣ ਅਤੇ ਇੱਕ ਸੁਰੱਖਿਅਤ ਕੰਮ ਕਰਨ ਵਾਲੇ ਵਾਤਾਵਰਣ ਨੂੰ ਯਕੀਨੀ ਬਣਾਉਣ ਦੀ ਕੁੰਜੀ ਹੈ।
ਪੋਸਟ ਸਮਾਂ: ਜਨਵਰੀ-12-2024